Contributing editor
- FMA
- The Fabricator
- FABTECH
- Canadian Metalworking
Categories
- Additive Manufacturing
- Aluminum Welding
- Arc Welding
- Assembly and Joining
- Automation and Robotics
- Bending and Forming
- Consumables
- Cutting and Weld Prep
- Electric Vehicles
- En Español
- Finishing
- Hydroforming
- Laser Cutting
- Laser Welding
- Machining
- Manufacturing Software
- Materials Handling
- Metals/Materials
- Oxyfuel Cutting
- Plasma Cutting
- Power Tools
- Punching and Other Holemaking
- Roll Forming
- Safety
- Sawing
- Shearing
- Shop Management
- Testing and Measuring
- Tube and Pipe Fabrication
- Tube and Pipe Production
- Waterjet Cutting
Industry Directory
Webcasts
Podcasts
FAB 40
Advertise
Subscribe
Account Login
Search
Prefinishing trends towards growth
No-muss, no-fuss technology blazes trails into new territories, gains ground in others
- By Kate Bachman
- October 12, 2004
- Article
- Finishing
New developments in coating compositions and new methods of applying the coatings have empowered precoated metal to blaze trails into new territories and to gain broader usage in familiar ones.
Boldly Going Where (Almost) No Coated Metal Has Gone Before
![]() |
Metal roofs can be roll formed or stamped to resemble traditional-looking shingles, clay tiles, wood shakes, and Victorian metal tiles. Photo courtesy of Metal Roofing Alliance, Belfair, Wash. |
Residential Metal Roofing. Residential roofing, traditionally constructed of asphalt shingles or clay tile, is increasingly being fabricated from precoated metal because of its energy conservation, fire resistance, and wind resistance.
Although metal roofing has been used for centuries in commercial and public buildings, its foray into residential applications is a 21st century phenomenon. The advent of new coatings with energy-saving properties has revolutionized the residential roofing industry with so-called "cool" metal roofing.
Prepaint coatings formulated for these cool metal roofing panels incorporate new "cool pigment" technology with high solar reflectance and high infrared emittance properties, according to the Metal Roofing Alliance and the Cool Metal Roofing Coalition, thereby saving energy by reducing a home's cooling needs.
According to the coalition, these cool roofs with specially formulated coatings and construction methods engineered to enhance solar reflectance and infrared emission properties meet the EPA's Energy Star® Roof Products Program performance criteria for reflectivity and have emissivity as high as 90 percent.
Ratings for reflectivity and emissivity range from 0 to 1. Typical 25-year gray asphalt shingles have a reflectivity of 0.09 and emissivity of 0.91. In comparison, white prepainted steel has a reflectivity of 0.64 and emissivity of 0.83, according to a report by the NCCA.
Generally, the coatings are composed of polyester and silicone resins, silicone-modified polymers (SMPs), or fluoropolymers. The polyester coatings are the least expensive and also the least durable. The fluoropolymers (fluroinated polymers) are at the other end of the quality scale, with good thermal- chemical-, and UV-resistant properties.
George Pilcher, technical director, coil and extrusion coatings, Akzo Nobel Coatings Inc., Columbus, Ohio, said the surging interest in residential metal roofing in the last three years has primarily been in response to legislative initiatives concerning energy conservation in California and Florida.
Currently metal roofing represents only 5 percent of all residential roofs, Pilcher said. The remaining 95 percent represents a vast opportunity for metal fabricators.
"It's still a small percentage of the marketplace now, but it's a huge marketplace," Pilcher said. "About 20 billion square feet of residential roofing is being installed in the U.S. every year."
Although the energy-conserving coatings can be applied in a postcoating process, almost all metal roofing panels are precoated, Pilcher said. "Basically, [new metal roofing] is a coil-coated industry," Pilcher said.
Niff-Corr LLC, Tippecanoe, Ind., has been fabricating residential prepainted steel roofing heavily for about five years, company president Hal Shafer said. "Demand is probably doubling every year."
Shafer said he believes that the reflectivity properties the coatings offer are only part of the reason for metal roofing's growth in residential applications. "It's basically a lifetime roof. The paint systems we have are 30-year-warranted systems, so people get a long life out of it."
In addition, the roofs can be roll formed or stamped to resemble traditional-looking shingles, clay tiles, wood shakes, and Victorian metal tiles. Shafer said that customers have a wide selection of colors to choose from and that he has gotten favorable responses from customers. "Everyone loves it. Once they put it on, they tend to fall in love with their metal roof."
![]() |
Ceiling panels, door hardware, refrigerators, dishwashers, sinks, and freezers can be fabricated from antimicrobial-coated steel. Photo courtesy of AK Coatings Inc. |
Making Inroads Into Offices, Health Care Facilities, HVAC. Coatings with antimicrobial agents are making coated coil more attractive for use in day care centers, office buildings, hotels, schools, and agricultural structures, as well as laboratories, medical facilities, and fitness centers.
The agents, such as AK Coatings Inc.'s AgION™ antimicrobial compound, suppresses the growth of bacteria, molds, fungi, and other microbes.
The terrorist anthrax threat has been cited as one of the main reasons for the increased interest in this compound, but the recent media exposure of health hazards created by some molds is another.
Although bed frames, cabinetry, furniture frames, lockers, bathroom fixtures, food processing equipment, appliances, and HVAC equipment often are already fabricated from metal coatings containing antimicrobial agents—pigmented or clear—have given reason for them to be fabricated of coated metal instead.
Because the coatings can be applied to either or both sides of coil, inaccessible areas of a fabricated part—such as the interiors of HVAC ductwork, hemmed edges, and tubes and profiles—can be coated with the agent as well.
If desired, a standard pigmented coating may be applied to one side of the coil and a clear epoxy coating containing the compound may be applied to the other side on a tandem coating line.
Automotive—The Final Frontier. The automotive industry is in their cross hairs, coil coaters say. To date, aluminum truck trailer bodies and automotive fittings and accessories such as bumper strips and interior trim sections are fabricated from prepainted strip.
Doug Bach, V.P., Advanced Technologies, DuPont Powder Coatings USA Inc., Houston, said he believes that precoated metal has potential for even broader application with automotive parts now being postpainted predominantly.
"That's an extra step, extra labor, extra handling. If you coat it in the flat coil form, you can streamline that process tremendously by not having to coat the part after it's formed," Bach said. "Interior parts, seat tracks, suspension parts, under-the-hood parts—all are good candidates for that."
"I'm convinced that coated coil is the wave of the future for automotive, but the auto industry itself has to decide that this is worth making some modifications," Pilcher said.
Pilcher concedes that issues like the exposed cut edge and alternative joining methods are considerations for coated coil's use in the automotive industry, but added, "These issues are important, but in my opinion, they shouldn't be deal breakers.
"If the cut edge proved to be a problem ... design changes would be made-the edge could be folded under, for example. Perhaps instead of welding, they would use adhesives, fasteners, or other joining methods," Pilcher said.
"There's a lot of progress to be made by using coil-primed metal in at least some portion of the automotive process," Pilcher said. He proposed that even if coil were only cleaned, pretreated, and primed with a weldable primer on a coil line before being shipped to an automotive fabricator for forming, stamping, and welding and a final topcoat applied, substantial tim and material savings could be realized.
"In other words, the automotive industry itself would have to adapt so that it could benefit from the efficiencies of using coil-coated metal," Pilcher said.
Robert McShane, president, First Precision LLC, a powder coil coating design firm in Chicago, called the automotive industry the "Holy Grail" for the coated coil industry, and predicted significant growth of coated coil in automotive.
"The reason I think this is going to happen is that the largest cost to an automaker is in his paint shop. His cost to assemble, put on tires doesn't even come close to what it costs to paint a car," McShane said. "So as automakers look at refining their cost structures, things that can reduce the activity in the paint shop are going to have a direct impact on the bottom line and dramatically reduce the amount of labor and time that go into making a car."
New Application Methods Gain Ground for Coated Coil
![]() |
Standing seam steel roofing is the most frequently used type of metal roofing. Coated coil panels are custom-cut to length and joined by interlocking or active fastening. Panel ends are attached to purlins under the roof structure, eliminating altogether the need for welding. Photo courtesy of Akzo Nobel Coatings Inc., Columbus, Ohio. |
Lisa Whirls, senior product specialist, prepainted steel, Ryerson Tull Coil Processing, Hamilton, Ohio, said she believes that many innovations related to coated metal are in the coatings application processes. "Things that are becoming trends now are more in line with cost containment ideas—using single primers regardless of the topcoat, or using more universal pretreatments."
New powder coil coating application processes that improve the coating's uniformity at nearly the same speeds as liquid coil coating systems may make powder-coated coil an attractive alternative to liquid-coated coil.
"Typically, the conventional powder-on-coil lines that exist today operate in the 50- to 60-feet-per-minute range," McShane said. "The powder is applied with a hand-held device, a powder gun that pneumatically conveys the powder and sprays it onto the surface. It works. The trouble is, you can't go real fast, and the coating is irregular and lumpy."
McShane said that First Precision's technology, PowderCoil™, employs an automatic device that causes the powder to act like a liquid. Like other powder coating systems, it pneumatically sprays powder across the width of a strip, but faster and more uniformly than hand-held powder systems, he said. "We're talking about targets in the 500-feet-per-minute range with this technology."
McShane said that the speed increase is attributable to improvements in the application process's reactivity and material flow—how fast the paint cures and the consistency of its texture.
Regarding the curing method, Bach said that powder coatings go through a chemical reaction when they are exposed to heat. "They start out as a plastic material, and when they are heated, they form a very tightly connected network of molecules. The cure is time- and temperature-dependent. The coatings have to be exposed for a certain amount of time at a certain temperature for that reaction to be totally completed."
Bach said that the powder coatings offer advantages over liquid coatings.
"The powder coatings exhibit excellent weatherability properties, superior corrosion protection properties, good formability, special effects such as multicolor coatings, textured coatings, metallic coatings, and antimicrobial-containing coatings." Bach added that the powder coatings can be used in some niche markets that liquid coatings may not be suitable for—on perforated metal, for example.
Adhesion Properties. Bach said that powder coatings can be applied directly to metal. "Powders inherently have very good adhesion properties. So it's a one-coat system that doesn't require primers or multiple coats of primers and topcoats."
Corrosion Properties. According to Bach, powder-coated coil has better corrosion resistance than liquid-coated coal. "Typical liquid paints have fluids in them that have to get out of the paint before it dries. And that process leaves voids—little channels where the liquid components escape to the surface, which is a path back down to the metal for a corrosion site."
"With powder coatings, there are no liquids coming off, therefore they melt, they flow, and they seal the surface," Bach said. "It's a very dense coating. You don't have the type of porosity you typically see with liquid coatings."
Bach added that conversion coatings still are required. "But instead of having two coats, three coats above the conversion coating, you'd have only one, in one pass."
Glossary Conversion Coating: A thin coating that converts a metal surface to a nonmetallic surface. It is formulated to enhance corrosion resistance, flexibility, paint durability, and adhesion. Emissivity: A measure of the thermal emittance of a surface; the ability of a material to emit heat (via infrared radiation) to the surrounding atmosphere. Reflectivity: A measure of the solar reflectance of a surface. A more reflective roof reflects the solar radiation away from the surface rather than absorbing it. |
Formability Improvements Set a New Course for Coated Coil
Many of the improvements in coil coatings technology are related to their formability.
"Let's say you're turning metal into a tube," McShane said. "It's one thing to bend uncoated or galvanized steel, but when you put paint on the surface, you can imagine how it has to stretch in order to make the bend. Or in stamping, when you put it through the die, there's deformation that takes place on the face and edges of the component. "Heretofore some of the painting systems applied to coil had poor performance," McShane said. "They looked great until you'd have to do a 0T bend. You could get a blush or a blur on the surface—not a radical change, but obviously that's a defect. So not only do you have to design the paint system to adhere and cure properly to the surface, but you have to put it through forming, so it is an issue."
McShane said that substantial developments in both liquid- and powder-coat chemistries have been made to increase formability. "Paint systems have come a long way to accommodate, in some cases, violent behavior, not only so you can bend it to shape, but also so it matches the color."
Bach said that both coatings types are formulated with enhanced formability properties, and added that most powder coatings are inherently formable.
"The powder coatings exhibit very good flexibility," he said. "They can achieve deep-draw forming, 2T, 1T, 0T bends."
When pressed to name the additives that increase formability, he revealed only "a secret recipe—back-burner coatings with very high-molecular-weight polymers that give a lot more flexibility."
Pilcher noted that increasing a coating's flexibility to improve forming can inhibit its ability to exhibit other properties, such as strength.
"Sometimes that flexibility brings along certain other, less desirableproperties with it," Pilcher said.
Because coated coil has so many different applications—building products for the outdoors, appliances exposed to harsh detergents, or drawn automotive parts—the coatings have different requirements, Pilcher said.
"They all require a different balance of formability, strength, and chemical resistance," Pilcher explained. "If building products, such as garage doors, are going to be outside, the coatings have to be resistant to the effects of humidity, acid rain, UV radiation, and so forth, but they also have to be formable enough to withstand embossing or stamping," he said.
Pilcher said that the coil industry has become more adept at balancing all of the requirements, which, in many cases, are contradictory—such as flexibility and hardness. "A lot of the work that's been done in the coil [coatings] industry in the last 20 years has been to make such requirements less and less incompatible."
Fasteners, Adhesives Come Along for the Ride
One of the net effects of the increased use of prepainted metal has been a corresponding increased demand for fasteners and bonded adhesives as alternatives to welding.
Dave Caulk, sales manager, AKH Inc., Indianapolis, said being able to offer the company's self-piercing fastener in a prepainted form to match the component has paved new avenues for the company.
"A lot of companies, especially in the appliance industry, are looking to eliminate the postpaint, so they're buying prepainted material and having a very difficult time joining the material. So we offer one of the leading options of doing that."
Editor's Note: For information on how to fabricate precoated metal, see "Working With Precoated Metal," which will be published in the December 2004 issue of The FABRICATOR®.
For information on coated coil in the automotive industry, see "'To Go' Prepainted Sheet Metal Accelerates Automotive Line Production" in the January 2004 issue of The FABRICATOR®, p. 52.
AK Coatings Inc., www.akcoatings.com
AKH Inc., www.akhfas-ner.com
Akzo Nobel Coatings Inc., www.akzonobel.com
Cool Metal Roofing Coalition, www.coolmetalroofing.com
DuPont Powder Coatings USA Inc., www.dupontpowder.com
First Precision LLC, www.powdercoil.com
Metal Roofing Alliance, www.metalroofing.com
National Coil Coating Association, www.coilcoat.org
Niff-Corr LLC, www.niffcorr.com
Ryerson Tull Coil Processing, www.ryersontull.com
About the Author
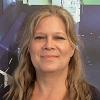
Kate Bachman
815-381-1302
Kate Bachman is a contributing editor for The FABRICATOR editor. Bachman has more than 20 years of experience as a writer and editor in the manufacturing and other industries.
subscribe now
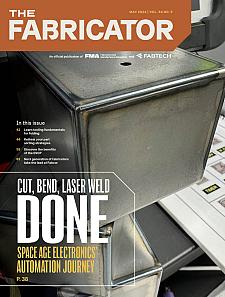
The Fabricator is North America's leading magazine for the metal forming and fabricating industry. The magazine delivers the news, technical articles, and case histories that enable fabricators to do their jobs more efficiently. The Fabricator has served the industry since 1970.
start your free subscription- Stay connected from anywhere
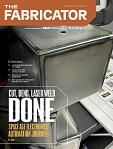
Easily access valuable industry resources now with full access to the digital edition of The Fabricator.
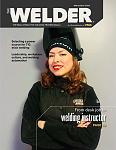
Easily access valuable industry resources now with full access to the digital edition of The Welder.
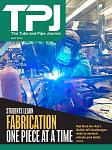
Easily access valuable industry resources now with full access to the digital edition of The Tube and Pipe Journal.
- Podcasting
- Podcast:
- The Fabricator Podcast
- Published:
- 04/16/2024
- Running Time:
- 63:29
In this episode of The Fabricator Podcast, Caleb Chamberlain, co-founder and CEO of OSH Cut, discusses his company’s...
- Industry Events
16th Annual Safety Conference
- April 30 - May 1, 2024
- Elgin,
Pipe and Tube Conference
- May 21 - 22, 2024
- Omaha, NE
World-Class Roll Forming Workshop
- June 5 - 6, 2024
- Louisville, KY
Advanced Laser Application Workshop
- June 25 - 27, 2024
- Novi, MI