- FMA
- The Fabricator
- FABTECH
- Canadian Metalworking
Categories
- Additive Manufacturing
- Aluminum Welding
- Arc Welding
- Assembly and Joining
- Automation and Robotics
- Bending and Forming
- Consumables
- Cutting and Weld Prep
- Electric Vehicles
- En Español
- Finishing
- Hydroforming
- Laser Cutting
- Laser Welding
- Machining
- Manufacturing Software
- Materials Handling
- Metals/Materials
- Oxyfuel Cutting
- Plasma Cutting
- Power Tools
- Punching and Other Holemaking
- Roll Forming
- Safety
- Sawing
- Shearing
- Shop Management
- Testing and Measuring
- Tube and Pipe Fabrication
- Tube and Pipe Production
- Waterjet Cutting
Industry Directory
Webcasts
Podcasts
FAB 40
Advertise
Subscribe
Account Login
Search
Laser welding aluminum
Meeting the challenge head-on
- By David Havrilla
- Updated October 26, 2023
- July 12, 2013
- Article
- Laser Welding
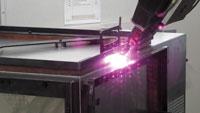
Properly addressing the troublesome attributes of aluminum and its alloys will help prevent potential issues during the laser welding process.
Editor’s Note: This article is based on David Havrilla’s presentation at the Aluminum Laser Welding Symposium, co-sponsored by TRUMPF Inc. and Fraunhofer USA in Plymouth Township, Mich.
Aluminum possesses many characteristics that make it an ideal material in the world of manufacturing. It has excellent corrosion resistance and is roughly one-third the mass of steel. This bodes well for the automotive industry in particular, which must increase fuel economy to a fleet average of 54.5 miles per gallon by 2025.
Aluminum’s other positive attributes include its high thermal conductivity—a very useful trait for heat exchangers and similar components—and its low electrical resistivity, which makes the metal a good current conductor and reinforces the versatility of the material. But these unique and useful attributes would be worthless if aluminum was not also easily formed, machined, and welded. Its manufacturability establishes aluminum as a highly desirable material for production.
The kicker, as many familiar with aluminum already know, is the material and its alloys have a few troublesome attributes that must be properly addressed to avoid potential problems during the welding process.
Problems and Solutions to Laser Welding Aluminum
With eight wrought alloy groups, the aluminum family can accommodate a wide variety of manufacturing applications (see Figure 1). Regardless of the alloy or application, the question of weldability inevitably arises. Luckily, most alloys can be successfully fusion welded, either with or without filler material. Joining with lasers can solve some of the problems that plague conventional welding techniques.
The wide range of temperatures in alloy vaporization and solidification can lead to keyhole instability, porosity, blowholes, a loss of mechanical properties, and various defects in the weld metallurgy such as hot cracking. The high rate of hydrogen solubility in molten aluminum can lead to extensive weld porosity and blowholes. The low viscosity of highly fluid molten aluminum can result in dropping or sagging of the underbead.
Finally, aluminum’s high reflectivity combined with its high thermal conductivity can lead to challenges with coupling of the light energy into the material. While this may sound dismal, the history and success of laser welding of aluminum is quite the opposite. Each characteristic and its related issues have a well-defined and production-proven solution. Let’s take a brief look at five of the most common issues, mechanisms, and control measures.
Hot Cracking, or Weld Solidification Cracking. This complication occurs because of solidification stresses on the microstructure and is worsened by aluminum’s high thermal expansion and conductivity. Hot cracking sensitivity often can be avoided by adding the appropriate filler wire or inlaid filler foil material, thereby altering the weld chemistry away from the crack-sensitive peak (see Figure 2). For example, standard values for good weldability are greater than 2 to 3 percent silicon and greater than 3 to 4 percent magnesium, yet the typical range in the 2000 and 6000 series aluminum alloys is between 0.4 and 1.6 percent. Therefore, these alloys usually require filler for crack-free welding.
The Presence of Hydrogen in Aluminum Laser Welding Hydrogen is abundant, especially in manufacturing environments, and its solubility in molten aluminum can lead to gross porosity. Water, lubricants, and air all contain the element, and although it readily dissolves into molten aluminum, it has virtually no solubility in solid aluminum. As a result, hydrogen in the molten weld pool is either trapped in the weld as pores, or it outgases, which causes blowholes upon solidification. Fortunately, some simple preventive measures can be taken to prevent hydrogen-related issues from occurring.
- Keep materials clean and dry, including the filler wire or foil.
- Avoid temperature differentials (e.g., storage to production area) that can cause condensation on the parts or filler material.
- Clean weld joints and remove porous oxides when needed.
- Use a shielding gas.
Porosity and Blowholes when Laser Welding These issues also can be caused by volatile alloying elements such as zinc, magnesium, and lithium. These elements vaporize, escape through the keyhole, and pull molten material along with them, leaving weld voids and spatter in their wake. The solution is to simply provide a large enough path (e.g., large focused spot size or tandem focus spot) or enough time (e.g., reduced weld speed) for the vapors to exhaust without causing damage.
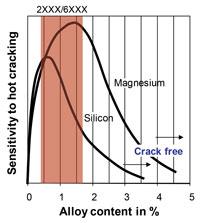
Figure 2: The graph shows the sensitivity to hot cracking versus the alloy content. The range of silicon and magnesium in 2000 and 3000 series aluminum is shown in red. Standard values for good weldability are greater than 2 to 3 percent silicon and greater than 3 to 4 percent magnesium, yet the typical range in the 2000 and 6000 series aluminum alloys is between 0.4 and 1.6 percent.
Underbead Dropping. This issue occurs in penetration welds of about 6 mm or more, though the exact thickness threshold depends on variables such as wavelength, alloy type, power, speed, and spot diameter. The simplest way to avoid it is to position the weld joint horizontally, but this is often impractical or impossible. When a vertical weld joint is necessary, there are several strategies that can be used to avoid underbead dropping in deep-penetration welding (see Figure 3):
- Use a partial-penetration weld.
- Redesign the component to avoid a through-penetration weld.
- Use an underbead backing material (e.g., copper).
Reflectivity in Aluminum Laser Welding In the past aluminum’s high reflectivity was a problem for laser welding. However, with the evolution of high-power, good-beam-quality carbon dioxide (CO2) lasers, and the advent of high-power, high-brightness solid-state, fiber-delivered lasers, coupling the energy into aluminum is no longer an issue.
These developments have led to a common misconception: Since the shorter-wavelength solid-state lasers, like disk and fiber, have a higher absorption into aluminum, they must be the best laser for all applications. This is not the case. For thicknesses up to about 4 or 5 mm, the 1-micron wavelength of the solid-state laser is preferred; however, when material thickness is 6 mm or more, the CO2 laser (10.6-micron wavelength) is the best choice. While the exact physics may be debated, an easy way to think about this is that due to the higher absorption of the 1-micron wavelength, a greater amount of the power is absorbed by the upper portion of the material. A 10.6-micron wavelength, however, is able to penetrate deeper into the material as it reflects down the keyhole.
Aluminum’s weight-to-strength ratio and corrosion resistance are two of the many reasons that manufacturers see it as a desirable material for their applications. While most aluminum alloys can be fusion welded, either with or without filler, there are a few well-known and -understood welding issues that can be easily overcome by production-proven methodologies.
To accentuate that reality, we need only look at the numerous aluminum and aluminum alloy components that have been laser welded for various industries since the 1990s. With the fuel economy mandates in automotive, light-weighting is a necessity, and aluminum is sure to be a significant part of that endeavor. With all its advantages and capabilities, laser joining these aluminum components is just as certain.
Aluminum: A History Lesson
Aluminum is a versatile metal with remarkable attributes. Its low atomic mass, high corrosion resistance, and excellent thermal and electrical conductivity make it a very unique material. It is easily machined, cast, drawn, and extruded—all appealing traits for manufacturers. Plus, there’s a lot of it. Next to oxygen and silicon, aluminum is the third most abundant element in the world and the most abundant metal, comprising more than 8 percent of the earth’s crust. Although plentiful, it is typically found in compounds, most often as the ore bauxite, rather than in its pure form. This has kept the resource largely untapped until the early 19th century, when scientists began to isolate and extract the metal.
Production of aluminum was still far from economically viable until the end of the century. In 1888 American chemist Charles Martin Hall formed the Aluminum Company of America (ALCOA) and within a year patented an inexpensive process to obtain aluminum from aluminum oxide using electrolysis. At the same time, French chemist Paul Héroult independently invented the same process, which became known as the Hall-Héroult method. In the same year, Austrian chemist Karl Bayer developed an inexpensive process for obtaining aluminum oxide from bauxite ore.
After the Bayer and Hall-Héroult processes were introduced and refined, the price of aluminum decreased drastically so that it was no longer considered a precious metal. Production of aluminum grew in popularity, and approximately 2 million metric tons were produced in 1943. In 2012, 46 million tons were produced, and it is estimated that by 2018 this number will grow to 71 million tons of aluminum.
About the Author
David Havrilla
47711 Clipper St.
Plymouth, MI 48170
734-454-7213
About the Publication
Related Companies
subscribe now
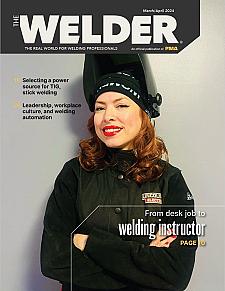
The Welder, formerly known as Practical Welding Today, is a showcase of the real people who make the products we use and work with every day. This magazine has served the welding community in North America well for more than 20 years.
start your free subscription- Stay connected from anywhere
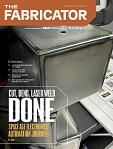
Easily access valuable industry resources now with full access to the digital edition of The Fabricator.
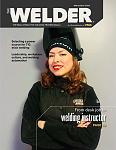
Easily access valuable industry resources now with full access to the digital edition of The Welder.
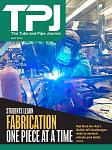
Easily access valuable industry resources now with full access to the digital edition of The Tube and Pipe Journal.
- Podcasting
- Podcast:
- The Fabricator Podcast
- Published:
- 04/16/2024
- Running Time:
- 63:29
In this episode of The Fabricator Podcast, Caleb Chamberlain, co-founder and CEO of OSH Cut, discusses his company’s...
- Industry Events
16th Annual Safety Conference
- April 30 - May 1, 2024
- Elgin,
Pipe and Tube Conference
- May 21 - 22, 2024
- Omaha, NE
World-Class Roll Forming Workshop
- June 5 - 6, 2024
- Louisville, KY
Advanced Laser Application Workshop
- June 25 - 27, 2024
- Novi, MI