Contributing Writer
- FMA
- The Fabricator
- FABTECH
- Canadian Metalworking
Categories
- Additive Manufacturing
- Aluminum Welding
- Arc Welding
- Assembly and Joining
- Automation and Robotics
- Bending and Forming
- Consumables
- Cutting and Weld Prep
- Electric Vehicles
- En Español
- Finishing
- Hydroforming
- Laser Cutting
- Laser Welding
- Machining
- Manufacturing Software
- Materials Handling
- Metals/Materials
- Oxyfuel Cutting
- Plasma Cutting
- Power Tools
- Punching and Other Holemaking
- Roll Forming
- Safety
- Sawing
- Shearing
- Shop Management
- Testing and Measuring
- Tube and Pipe Fabrication
- Tube and Pipe Production
- Waterjet Cutting
Industry Directory
Webcasts
Podcasts
FAB 40
Advertise
Subscribe
Account Login
Search
Die Science: Step-by-step troubleshooting of stamping dies, Part I
Identifying problems and verifying die setup
- By Art Hedrick
- March 6, 2015
- Article
- Bending and Forming
Opinions on how to troubleshoot a stamping operation are not in short supply at any production stamping or die-building shop. I’m not trying to stereotype diemakers, designers, or technicians, but their decisions often are made based on insufficient data.
Statistically speaking, if I presented a stamping-related part failure, such as a split, to five typical diemakers, I would probably get five opinions regarding the best corrective action to take. One would blame the coil material, one would blame the press operator, one would blame the die designer, one would blame the lubricant, and the last one would blame the poor die maintenance methods that took place during the other shift.
Sound familiar? You’re not alone. I might sound harsh, but based on more than 30 years in the die business, it is my strong opinion that there is a definite lack of data in the metal stamping and die-building industry. We often make decisions based on the way we learned the trade, or because it worked last time, or because “that’s how we do it here.”
I’m not saying that making decisions based on past experience causes failure, but I am asking, Where’s the data?
Are stampers and die builders expected to make changes to the process based on experience? It’s a hard pill to swallow, but if I’m completely honest with myself, my years of die experience are of little value to me. It’s what I have learned in my past that’s of value, not the time I’ve spent. Thirty, 40, or even 50 years of making poor decisions based on insufficient data doesn’t add up to much value.
The key is to understand why failures occur and to support your corrective decisions with data, not opinions. To do this, you can use a simple, multistep troubleshooting process, tailoring it for your resources, operating procedures, and die creation.
Step 1—Identify Part Problems
Identifying part problems is usually fairly easy. These can include splitting, cracking, nonconforming part geometry, wrinkling, loose metal, understrained parts, excessive burrs, scratches, dents, slug depressions, and score marks.
The person inspecting the part needs to have a clear understanding of each type of failure and be able to communicate it clearly to the person responsible for correcting the problem.
Step 2—Verify That the Die Is Set up Properly
Very often stampers make major changes to a die, only to find out the die was not set up correctly in the first place. Here are a few basic things to check:
- Verify the die shut height, stop block lead readings, and press tonnage readings. If you are using bottom makers, verify that they are visible and to the correct depth in the part and/or scrap.
- Make sure the die is tight against the positive location stops and is parallel to the coil.
- Verify that the lubricant application method is correct, ensure the die and metal are getting lubricated as necessary, and make sure all sprayers and rollers are working properly.
- Check the thickness, width, and metal mechanical properties of the incoming coil material.
- Verify the pilot and feed release timing on progressive dies.
- Make sure the feed distance (pitch) is set correctly.
- Ensure that pressure systems, such as nitrogen systems, press cushions, and hydraulic pressure systems, are charged to the correct operating pressure.
- Verify that the die is flush with the bolster plate and ram. Make sure there is no debris underneath the die shoes, castings, or plates.
- Check all remaining press parameters, such as counterbalance and clutch pressure.
- Make sure all locators and gauges are in their correct positions and that the blank is being properly located.
- Verify that there are no pieces of loose scrap, slugs, or obstructions in the die.
- Ensure the coil material is being adequately straightened, leveled, and flattened before entering the die. Periodic adjustments in the straightening equipment might be needed during production.
- Make sure scrap and slugs falling from the die are being carried away properly and that all slug shuts and shakers are functioning correctly.
- Verify that all bolts securing the die in the press are tight.
As much as I like to present data based on an understanding of sheet metal physics and dies, occasionally I still find myself standing at the press scratching my head and asking myself, What in the world is going on here?
The key is to eliminate systematically, one by one, all of the controlling variables. Only then can you say, “Based on the data presented or discovered, it is my opinion that ….”
I’ll present the rest of the troubleshooting steps in Part II, which will appear in the March/April issue.
About the Author
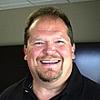
Art Hedrick
10855 Simpson Drive West Private
Greenville, MI 48838
616-894-6855
Related Companies
subscribe now
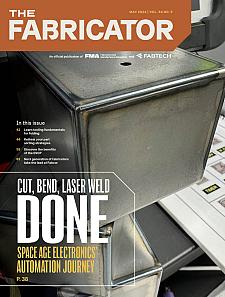
The Fabricator is North America's leading magazine for the metal forming and fabricating industry. The magazine delivers the news, technical articles, and case histories that enable fabricators to do their jobs more efficiently. The Fabricator has served the industry since 1970.
start your free subscription- Stay connected from anywhere
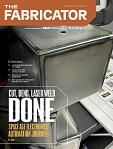
Easily access valuable industry resources now with full access to the digital edition of The Fabricator.
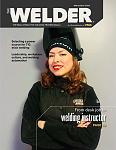
Easily access valuable industry resources now with full access to the digital edition of The Welder.
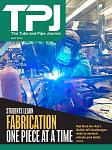
Easily access valuable industry resources now with full access to the digital edition of The Tube and Pipe Journal.
- Podcasting
- Podcast:
- The Fabricator Podcast
- Published:
- 04/16/2024
- Running Time:
- 63:29
In this episode of The Fabricator Podcast, Caleb Chamberlain, co-founder and CEO of OSH Cut, discusses his company’s...
- Trending Articles
Capturing, recording equipment inspection data for FMEA
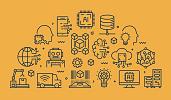
Tips for creating sheet metal tubes with perforations
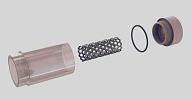
Are two heads better than one in fiber laser cutting?
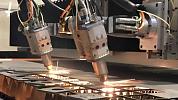
Supporting the metal fabricating industry through FMA
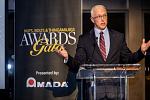
Omco Solar opens second Alabama manufacturing facility
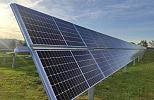
- Industry Events
16th Annual Safety Conference
- April 30 - May 1, 2024
- Elgin,
Pipe and Tube Conference
- May 21 - 22, 2024
- Omaha, NE
World-Class Roll Forming Workshop
- June 5 - 6, 2024
- Louisville, KY
Advanced Laser Application Workshop
- June 25 - 27, 2024
- Novi, MI