Senior Editor
- FMA
- The Fabricator
- FABTECH
- Canadian Metalworking
Categories
- Additive Manufacturing
- Aluminum Welding
- Arc Welding
- Assembly and Joining
- Automation and Robotics
- Bending and Forming
- Consumables
- Cutting and Weld Prep
- Electric Vehicles
- En Español
- Finishing
- Hydroforming
- Laser Cutting
- Laser Welding
- Machining
- Manufacturing Software
- Materials Handling
- Metals/Materials
- Oxyfuel Cutting
- Plasma Cutting
- Power Tools
- Punching and Other Holemaking
- Roll Forming
- Safety
- Sawing
- Shearing
- Shop Management
- Testing and Measuring
- Tube and Pipe Fabrication
- Tube and Pipe Production
- Waterjet Cutting
Industry Directory
Webcasts
Podcasts
FAB 40
Advertise
Subscribe
Account Login
Search
Quality springs forward with 3-D printing
Spring-maker/stamper uses additive manufacturing to improve quality assurance
- By Tim Heston
- January 29, 2015
- Article
- Testing and Measuring
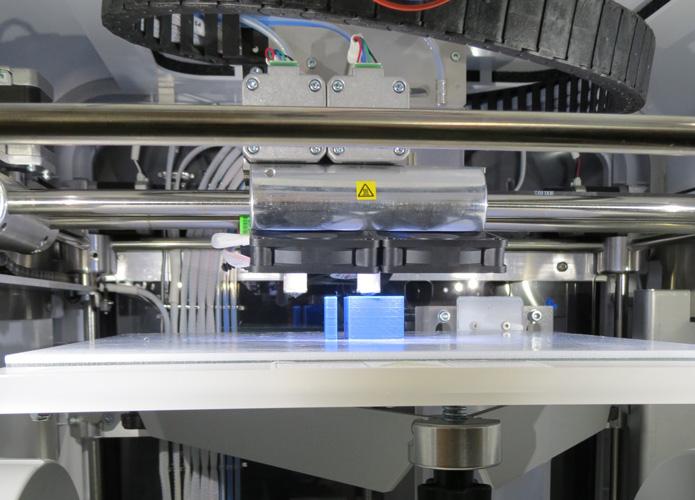
Figure 1
Newcomb Spring’s 3-D printer builds up a fixture component
(blue in the photo), layer by layer.
The thinking goes that our grandchildren will look back at the early 2000s as a quaint time when companies actually made things by cutting and shaping them out of larger elements, be it by machining a rough casting or cutting a blank out of a larger piece of sheet metal. Why go through the trouble? Why not build up the part, layer by layer?
Additive manufacturing is making its mark in the machining world. Hybrid systems now allow machinists to mill or turn a component—a subtractive process—then build up certain areas via an additive process. In sheet metal forming and fabricating, additive manufacturing has piqued interest, but it still takes time for an additive process to build up a component layer by layer, while a stamping press still can blank and form a sheet metal part in a matter of seconds.
So why exactly has Newcomb Spring Corp., a 400-employee spring-maker and stamper with nine locations in North America, embraced additive manufacturing? Don Jacobson III, technical salesperson at Newcomb’s Ooltewah facility, outside Chattanooga, Tenn., pointed to a small sheet metal part that was stamped on a four-slide machine. Its odd shape prevented it from lying flat, which meant that the quality department had to build a fixture to measure it.
Today an engineer designs a fixture in CAD and exports it to the 3-D printer in the next room (see Figure 1). In short order he has a fixture capable of holding the small component at the correct orientation for the quality department. It boils down to saving time, and 3-D printing saves plenty of it, not for the actual stamping or spring-making, but the steps that support those core manufacturing processes.
High-value Springs and Stampings
Ooltewah has grown tremendously during the past few years. New construction is everywhere. Driving along Tennessee Route 321, you can see rustic barns next to mini-mansions and other new construction, much of it brought about by the nearby Volkswagen plant.
Newcomb’s Tennessee facility sits on a hillside on what was a residential road. In fact, decades ago the Newcomb facility was a residence. In the early 20th century, a spring-maker retired and moved to what was then rural Appalachia.
“He loved the area, but he also wanted to get back into the spring business, so he opened up a facility behind his house. He was a friendly competitor, and 47 years ago he wanted to retire—for real this time—so Newcomb purchased the facility from him,” Jacobson said, whose great-grandfather, George Jacobson, helped launch Newcomb in the 1920s.
Newcomb Spring has grown not by offering millions of a certain spring or stamping; that commodity work has moved overseas. It instead has specialized in lower-volume work, measured in thousands instead of millions of parts a year, and much of it requires a lot of upfront design and prototyping. Customers range from small start-up companies to major players in power generation, automotive, aerospace, lawn equipment, and other sectors.
Maintaining a competitive edge has required continual scrutiny to increase efficiency and quality. The company designs proprietary spring-making machinery to eliminate or reduce the number of secondary operations and ensure quality. Such machinery has streamlined production significantly, but until six years ago, inefficiencies remained in a small but critical department: quality assurance.
Efficiency in Quality
Quality Engineer Daniel Lewis walked toward what looked like a small refrigerator, only it wasn’t a fridge. It was a 3-D printer, a CubePro® Duo made by 3D Systems of Rock Hill, S.C. As its name implies, the printer can deposit two different materials at once, and two different colors. It can process several types of plastic (including polylactic acid, or PLA, and acrylonitrile butadiene styrene, or ABS), as well as nylon. Lewis hit a few buttons to call up a job, and in about 30 minutes the system printed a fixture with a side support and several posts. He inserted the part, which fit neatly inside (see Figures 2-4).
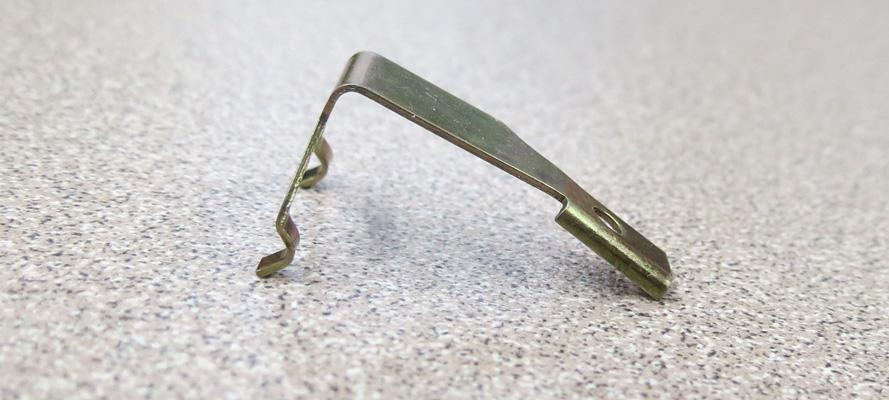
Figure 2
This stamped component doesn’t lie flat, so it needs a
custom fixture to be measured. That’s where 3-D printing
comes into play.
This in a nutshell is how 3-D printing goes hand in hand with stamping and spring-making at Newcomb. The system prints the fixtures that hold parts so that Newcomb’s measuring machines can inspect them efficiently and accurately.
“Traditionally, when inspecting a piece like this, you have to orient it by hand to several different positions,” Lewis explained, “which has room for error in and of itself. And when you measure each piece, a lot of time is consumed, which slows down the quality and manufacturing process as a whole. That’s not a good thing when you’re trying to get parts out the door.”
“We didn’t know we needed a 3-D printer until we began researching advanced measuring equipment,” Jacobson added. “That’s where it started.”
The Road to Additive Manufacturing
Six years ago quality personnel still used an optical comparator to check the angles and radii of all stamped components and springs. It was a manual machine. Technicians had to manipulate the table, bring the part into focus, measure each attribute, then reorient the part to measure other attributes. A comparator still makes sense if parts are simple or the number of pieces requiring inspection is low compared with the overall job size. But for Newcomb’s sweet spot—complex low- and medium-volume work—the company needed something better. The manufacturer may need to perform production part approval processes (PPAPs) on dozens of components for a single job, and for this an optical comparator made tedious work.
So Newcomb upgraded to an automatic video-based inspection and measurement system, a machine that effectively removed the tedium. The technician uses a joystick to zoom in and out, and the cameras measure in the X, Y, and Z planes. To check dozens of components, he places the part on a fixture, and the system takes the necessary measurements. He then removes the part and places the next part into the fixture.
It works wonders if a technician needs to check many parts in a run, especially if a customer provided the fixture. Its sensors measure from above and below, so with the right program and fixture, a technician need not reorient a part to capture multiple data points. The company also developed fixtures out of LEXAN™, a clear material that allows the 3-D system to measure parts from below the workpiece.
Nevertheless, a tech using this newer system still needs the right program and fixture, and each can take serious time to develop. The tech also needs to place the part in the same orientation on the bed every time. If he needs to juggle multiple jobs over the workday, as is common for contract manufacturers and job shops, he can spend a lot of time machining fixtures and programming the inspection machine, and not enough time actually measuring parts.
“We were trying to run every job that came in on this system,” Jacobson said, “but we were having to spend anywhere from an hour to four hours writing a program, plus the time we needed to make the fixture. That’s not really practical for our operation. It’s nice to think that you’ll have a job in perpetuity, but we’re not guaranteed it. We’re guaranteed a certain amount of parts at a certain price delivered on certain dates.”
Quality technicians needed an alternative, and they found one. Called Instant Measurement, or IM, the system from Keyence Corp. doesn’t require extensive programming. Unlike the company’s previous system, the IM machine measures from overhead only. Using a proprietary pattern analysis tool it scans and locates the part no matter where it’s placed in the work envelope, and compares it with information exported from the 3-D model. The system can measure multiple parts at once, as long as they’re the same part, and they all fit within the work envelope.
The 4- by 8-inch worktable moves under the camera, which can view an area that’s about 4 by 4 in. “The base can move and stitch together an image that is 4 by 8 inches,” Jacobson said, “and we can stitch together multiple 4-by-8 measurements to check larger parts.”
A green notation on the screen shows that the part is within tolerance, red means it’s out of tolerance, and each point is measured as part of a system. One radius may be within a specified tolerance, but if it’s off enough to throw another radius out of tolerance, the system flags the error. It can also measure multiple parts simultaneously as long as they all fit in the work envelope (see Figure 5).
The quality technician now could place a part anywhere in the work envelope, and he didn’t need to spend hours programming inspection routines for each part. This eliminated a lot of setup time. Still, one hurdle remained—the fixturing—because the overhead camera needed to be able to see certain features. If a technician couldn’t set a part in a way that presents the features clearly to the overhead camera, he still needed to build a fixture.
The same applied to components that must be measured in a certain condition. For instance, Lewis pointed to a bracket with a profile simple enough that you might think it could be placed on its side to measure it. But the bracket needed to be measured as part of a subassembly, bolted onto another component, which stretched the bracket slightly. To simulate this in-service condition again required a fixture.
Enter 3-D printing. Last year the company invested in its 3-D printer, sold and serviced through NovaCopy, which has a branch near Newcomb’s Tennessee operations. “We wanted to do work with a local company that had a local representative,” Jacobson said. “You can buy these printers through Amazon and Home Depot, but 3-D printing is still a developing industry in general, so it helps to have local customer service.”
It can take anywhere between 30 minutes to two and a half hours to build a fixture, depending on the material thickness and density. “Most initial items are run at a lower quality scale and with the highest speed to check the design,” Jacobson said. “Once we have a fixture or item we like, we build the item in the highest quality and thickness density.”
Some fixtures are quite complex, with multiple supports and posts; others are simple. For instance, to measure its in-service condition, a technician bolts a bracket to a 3-D-printed block with two threaded holes.
Of course, the beauty of 3-D printing is that making a highly complex workpiece isn’t cost-prohibitive. The system doesn’t care how many posts, supports, crevices, contours, or other complexities a workpiece has.
Printing for Prototypes
Most work sent to the 3-D printer heads to the quality lab, but not all of it. Jacobson pointed to a 3-D-printed block with several threaded holes. The block is being used in a spring-making machine prototype. Although Newcomb buys many of its machines, it also custom-builds some proprietary spring-making machines for certain jobs. This has been a key competitive advantage, and 3-D printing has helped streamline the process.
Finally, 3-D printing has helped in prototyping and product development. As Jacobson explained, “A lot of our customers are inventors or part of small start-ups, and they don’t have the resources available to do a lot of prototyping and testing. So we’re able to help them along the way.” He added that a spring or stamped component may fit into a larger subassembly, so the company often 3-D prints the mating components to ensure the spring or stamping fits and works as it should.
Outside its Tennessee plant, Newcomb has another 3-D printer at its Dallas facility, and it’s looking to add more printers in the future as more projects require them. In addition, every Newcomb plant has an IM system to measure parts.
“Because we’re a metal manufacturer, if we need something made, we make it out of metal,” Jacobson said. “It’s not always the cheapest, fastest, or most forgiving way to go.” This includes prototypes and fixtures for inspection. In effect, the 3-D printing system has allowed Newcomb to quickly make components that don’t necessarily need to be made out of metal.About the Author
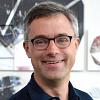
Tim Heston
2135 Point Blvd
Elgin, IL 60123
815-381-1314
Tim Heston, The Fabricator's senior editor, has covered the metal fabrication industry since 1998, starting his career at the American Welding Society's Welding Journal. Since then he has covered the full range of metal fabrication processes, from stamping, bending, and cutting to grinding and polishing. He joined The Fabricator's staff in October 2007.
Related Companies
subscribe now
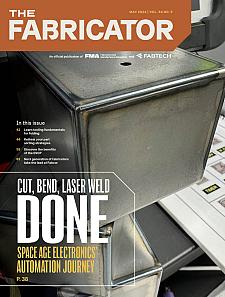
The Fabricator is North America's leading magazine for the metal forming and fabricating industry. The magazine delivers the news, technical articles, and case histories that enable fabricators to do their jobs more efficiently. The Fabricator has served the industry since 1970.
start your free subscription- Stay connected from anywhere
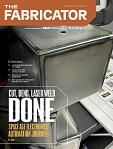
Easily access valuable industry resources now with full access to the digital edition of The Fabricator.
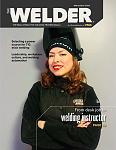
Easily access valuable industry resources now with full access to the digital edition of The Welder.
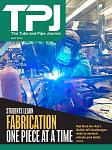
Easily access valuable industry resources now with full access to the digital edition of The Tube and Pipe Journal.
- Podcasting
- Podcast:
- The Fabricator Podcast
- Published:
- 04/16/2024
- Running Time:
- 63:29
In this episode of The Fabricator Podcast, Caleb Chamberlain, co-founder and CEO of OSH Cut, discusses his company’s...
- Trending Articles
Capturing, recording equipment inspection data for FMEA
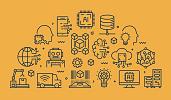
Tips for creating sheet metal tubes with perforations
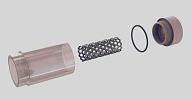
Are two heads better than one in fiber laser cutting?
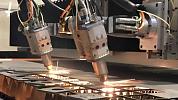
Supporting the metal fabricating industry through FMA
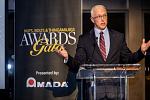
Omco Solar opens second Alabama manufacturing facility
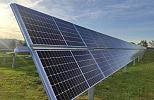
- Industry Events
16th Annual Safety Conference
- April 30 - May 1, 2024
- Elgin,
Pipe and Tube Conference
- May 21 - 22, 2024
- Omaha, NE
World-Class Roll Forming Workshop
- June 5 - 6, 2024
- Louisville, KY
Advanced Laser Application Workshop
- June 25 - 27, 2024
- Novi, MI