Senior Editor
- FMA
- The Fabricator
- FABTECH
- Canadian Metalworking
Categories
- Additive Manufacturing
- Aluminum Welding
- Arc Welding
- Assembly and Joining
- Automation and Robotics
- Bending and Forming
- Consumables
- Cutting and Weld Prep
- Electric Vehicles
- En Español
- Finishing
- Hydroforming
- Laser Cutting
- Laser Welding
- Machining
- Manufacturing Software
- Materials Handling
- Metals/Materials
- Oxyfuel Cutting
- Plasma Cutting
- Power Tools
- Punching and Other Holemaking
- Roll Forming
- Safety
- Sawing
- Shearing
- Shop Management
- Testing and Measuring
- Tube and Pipe Fabrication
- Tube and Pipe Production
- Waterjet Cutting
Industry Directory
Webcasts
Podcasts
FAB 40
Advertise
Subscribe
Account Login
Search
2023 FAB 40: Performance brings opportunity for metal fabricator BTD
Minnesota manufacturer continues to ramp up its automation initiatives
- By Tim Heston
- June 8, 2023
- Article
- Automation and Robotics
Visit a BTD plant, and you might witness a team of people walking the floor, sitting in a conference room discussing part flow, and discussing how to make work more productive, especially for employees on the front line. The team is dedicated to automation, and they’ve become critical to BTD’s operation in recent years.
“Our dedicated automation team constantly looks at our operation. We’re investing between $17 million and $20 million annually [in capex], and I would say that nearly a third of that investment is automation related.”
That was Jared Lotzer, vice president of commercial operations and business development at the Detroit Lakes, Minn.-based fabricator, which operates as an independent subsidiary of Otter Tail Corp., a publicly traded company. In recent years, the operation has performed its own integration of automation—an approach that has helped the company succeed during an acute labor shortage in an inflationary era. Like any fabricator, BTD—even with $350 million in annual revenue and five plants spanning the Midwest and Southeast—can’t automate its way out of every problem, but it remains a key part of the solution.
This year, BTD lands at No. 3 on the FAB 40 list.
Key Areas of Automation
Considering BTD’s size, not to mention its extensive toolmaking capability, Lotzer said that bringing the integration function in-house just made sense.
A BTD plant might have robotic arms feeding stamping presses, operating press brakes, and carrying pieces between different operations like riveting and spot welding. And the tooling those machines and robot arms use aren’t off-the-shelf. “Having more than 100 toolmakers on staff helps,” Lotzer said, adding that such tooling talent collaborating with the company’s in-house automation experts creates some unique solutions.
“We’re also now looking into building our own arc welding cells,” Lotzer said, ones tailored for BTD’s typical part geometries. “We’re taking a different stab at the automation challenge. We now have almost 30 robotic weld cells. We’re trying to migrate away from hand welding as much as we can. We used to say, ‘If the job isn’t more than 3,000 pieces, we’re not putting in a robot welder.’ But with some of these cobots and the new programming technology that’s available, we’re now processing low volumes in our automated weld cells. We just didn’t see that years ago. We couldn’t justify the cost. That’s now changed, and we’re getting better and better at it.”
The team has developed unique approaches to programming, complete with offline simulation. “[Integrating automation in-house] also has to do with speed,” Lotzer said. “When we determine we’re going to buy a piece of capital and put automation in front of it, we need to move quickly.”
The team has tailored automated cells to work with specific gauges and part sizes that are common within BTD’s product mix. In some cells, a robot arm performs multiple functions. In other cases, due to part geometry or weight, a robot arm performs specific tasks in concert with another arm or other pieces of automation.
Lotzer added that of course not every job can be automated; that’s a reality of contract fabrication. Still, automation has become more intertwined with the overall business. And it’s not as if BTD doesn’t need more people. At one point this year, the fabricator had more than 100 open positions, many of them for manual operations.
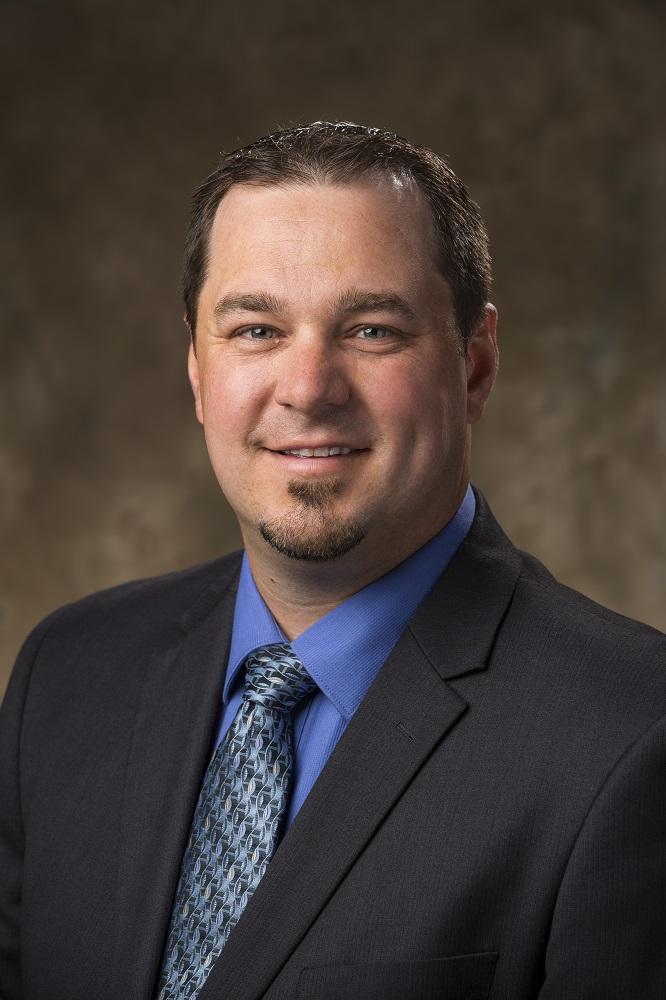
Jared Lotzer, vice president of commercial operations and business development, explained how challenges throughout the supply chain have led to variations in customer take rates of BTD’s finished-goods inventory.
Still, the cost-benefit analysis of automation has changed, and if a robot or other form of automation can eliminate a mundane task, so much the better. Moreover, the automation team talks with supervisors and operators about specific tasks and collaborates with them to improve.
About Response
The automation has been designed to help BTD respond quickly to changes in customer demand. Again, most automation isn’t product-specific but instead designed around material thickness and geometry, including part size, that the fabricator typically processes.
Like other fabricators, BTD had to overcome a number of supply chain challenges during the pandemic, including wide swings in “take rate,” or the rate at which OEM customers drew less from BTD’s finished-goods inventory. Early on in the pandemic, BTD put on the brakes, stopped hiring, and drew down its inventory.
Then, by the middle of 2022, the take rates rebounded—big time—as did new opportunities. “By the middle of 2022, our awarded business was at an unprecedented level,” Lotzer said. At that point, BTD’s model of managing those finished-goods inventories was a big selling point for clients scrambling to deal with shortages. That increased demand, though, reduced BTD’s inventory to a level where the fabricator had to begin hiring again.
“It’s been a bit of a roller coaster,” Lotzer said, “but we still believe in the business model. On-time delivery is king in this space. In this business, performance equals opportunity. And when it comes to new part programs, we come with a proposal with automation in mind.”
The model is proving successful, judging by BTD’s expansion plans. At this writing, the company is preparing to greatly increase its manufacturing space in the Southeast, complementing its existing plant in Dawsonville, Ga., just north of Atlanta. Lotzer said more details on the expansion should emerge later this year. Even with existing capacity in Georgia, “we still ship a lot of products from the Midwest to the Southeast,” Lotzer said. “There’s just so much opportunity there.”
When new opportunity comes, customers often visit a BTD plant to see automation in action. They witness how well-designed cells increase throughput, make manufacturing cycle times predictable, and improve quality. Sure, quality can’t be “inspected into” the process, whether it’s automated or not. But automating inspection helps eliminate ambiguity. “You don’t have a person missing something or interpreting something incorrectly,” Lotzer said.
This isn’t to say QA personnel aren’t conscientious, but at the same time, inspection can be repetitive and tedious. The same goes for other jobs, like production welding or material handling. The more tedious a job, the less engaged people can be.
Fabricators can’t automate every manual task, and when they ignore the human element, problems arise and throughput suffers. An automated fab shop still needs someone to move and present the material and, not least, manage and maintain the automation. After all, an automated plant’s throughput can be extraordinarily high one day and then grind to a halt the next—all because the company failed to properly manage and maintain their automated systems. Think of automated cutting systems crashing as cut parts become welded to dirty slats, or rework rising because someone didn’t properly align or clean a cutting head.
To prevent all this, BTD today has developed new career paths. Someone might start as a machine operator but over time might become an automation technician, trained to operate and maintain specific systems. For instance, a press brake operator might be trained to run an automated bending cell. With further training, he might be promoted to “Automation Tech II,” a position that’s responsible for running, setting up, and programming a robotic cell.
“And from there, these operators could move up to one of our integration teams,” Lotzer said, adding that not everyone on their automation teams need to be a degreed engineer. He added that people with shop floor experience can be extraordinarily valuable when automating a process. They know what challenges they faced, be it manipulating workpieces between staged tools on a press brake or accessing a joint for welding. All this gives them a fresh perspective on automated solutions—what’s needed, what could go wrong, what tasks could be eliminated altogether, and what could make an operation more productive than ever.
Assembling the Future
Just as BTD is dealing with labor shortages, so are its customers. So, it’s no surprise they’re relying on suppliers to add more value, including assembly. “We’re doing more and more value-added assembly,” Lotzer said. “We have more rubber, foam, and other material being brought in and assembled to our core metal products.”
With this comes more responsibility in supply chain management and risk mitigation, including dual sourcing, which requires BTD’s purchasing team to step up. The company has experienced supply chain challenges like anyone else: Hydraulics were a challenge early in the pandemic; now, specialty raw material is tough to find.
Lotzer said that the team is adapting to an ever-changing, dynamic supply chain. They’re working to ensure sufficient safety stock levels, both in-house and at vendor facilities. “We have products out there now that have eight-month lead times. You just didn’t experience that prior to the pandemic.”
He then referred back to BTD’s growth—for certain sectors it’s 20% or more, year over year, in the first quarter—and again to its expansion plans in the Southeast. That growth hinges on the fabricator’s ability to maintain its finished goods stock—enough to maintain stellar delivery performance and deal with variations in supply, but not so much as to tie up too much cash and drain resources. Cash is much better spent on something productive, like people or machinery, not idle inventory—even in this post-pandemic, just-in-case manufacturing world.
Published every June, the FAB 40 features some of the largest custom metal fabricators in the United States. Click here to learn more and to see this year's ranking.
About the Author
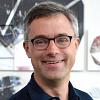
Tim Heston
2135 Point Blvd
Elgin, IL 60123
815-381-1314
Tim Heston, The Fabricator's senior editor, has covered the metal fabrication industry since 1998, starting his career at the American Welding Society's Welding Journal. Since then he has covered the full range of metal fabrication processes, from stamping, bending, and cutting to grinding and polishing. He joined The Fabricator's staff in October 2007.
Related Companies
subscribe now
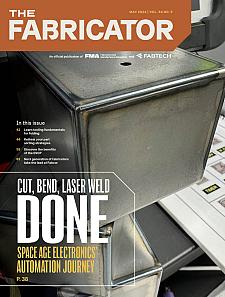
The Fabricator is North America's leading magazine for the metal forming and fabricating industry. The magazine delivers the news, technical articles, and case histories that enable fabricators to do their jobs more efficiently. The Fabricator has served the industry since 1970.
start your free subscription- Stay connected from anywhere
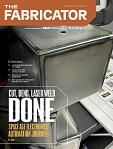
Easily access valuable industry resources now with full access to the digital edition of The Fabricator.
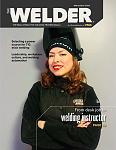
Easily access valuable industry resources now with full access to the digital edition of The Welder.
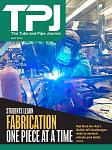
Easily access valuable industry resources now with full access to the digital edition of The Tube and Pipe Journal.
- Podcasting
- Podcast:
- The Fabricator Podcast
- Published:
- 04/16/2024
- Running Time:
- 63:29
In this episode of The Fabricator Podcast, Caleb Chamberlain, co-founder and CEO of OSH Cut, discusses his company’s...
- Trending Articles
Tips for creating sheet metal tubes with perforations
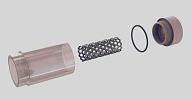
JM Steel triples capacity for solar energy projects at Pennsylvania facility
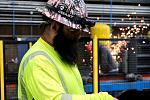
Are two heads better than one in fiber laser cutting?
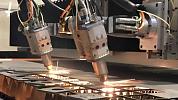
Supporting the metal fabricating industry through FMA
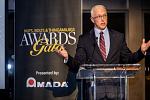
Omco Solar opens second Alabama manufacturing facility
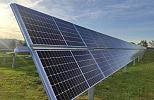
- Industry Events
16th Annual Safety Conference
- April 30 - May 1, 2024
- Elgin,
Pipe and Tube Conference
- May 21 - 22, 2024
- Omaha, NE
World-Class Roll Forming Workshop
- June 5 - 6, 2024
- Louisville, KY
Advanced Laser Application Workshop
- June 25 - 27, 2024
- Novi, MI