Editor-in-Chief
- FMA
- The Fabricator
- FABTECH
- Canadian Metalworking
Categories
- Additive Manufacturing
- Aluminum Welding
- Arc Welding
- Assembly and Joining
- Automation and Robotics
- Bending and Forming
- Consumables
- Cutting and Weld Prep
- Electric Vehicles
- En Español
- Finishing
- Hydroforming
- Laser Cutting
- Laser Welding
- Machining
- Manufacturing Software
- Materials Handling
- Metals/Materials
- Oxyfuel Cutting
- Plasma Cutting
- Power Tools
- Punching and Other Holemaking
- Roll Forming
- Safety
- Sawing
- Shearing
- Shop Management
- Testing and Measuring
- Tube and Pipe Fabrication
- Tube and Pipe Production
- Waterjet Cutting
Industry Directory
Webcasts
Podcasts
FAB 40
Advertise
Subscribe
Account Login
Search
Making spiral fabrication more predictable
A section bending machine gives fab shops the capability to produce these challenging forms
- By Dan Davis
- March 12, 2021
- Article
- Bending and Forming
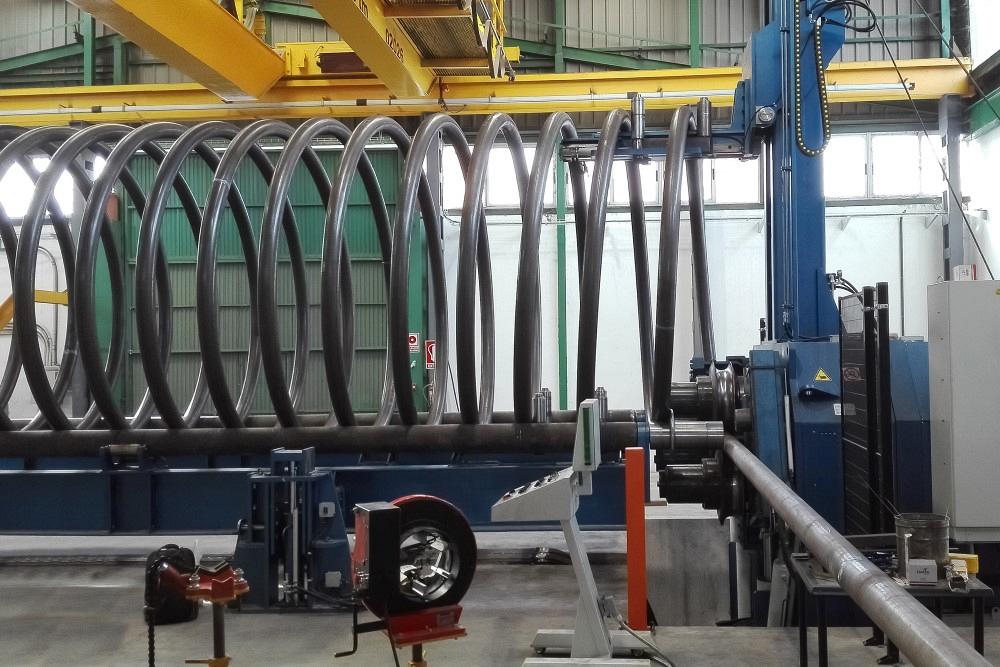
A section bending machine has to be precise when forming spirals because you can’t go back for another pass with this sort of bending application.
You might think fabricating spirals is something that can be done only by a craftsman with years of experience and an incredible attention to detail. That’s not necessarily the case.
Spiral production can be done consistently and accurately with the help of the right tools. This has been proven out by metal fabricators serving industries, such as power plants, petrochemical production facilities, food manufacturers, and manufacturers of industrial heating and cooling products.
But it’s not just the large manufacturers that use this type of technology. It’s also used by the craftspeople who fabricate staircases and handrails. In all these instances, the fabricators need to meet exacting specifications so that the end product is not only visibly acceptable, but also delivers on the original design intent.
Just think of the complexity involved in fabricating a single heat exchanger that has two spirals, either a smaller one surrounded by a bigger one or two spirals of the same diameter and pitch that are inserted one inside the other. The final spiral fabrications have to meet predetermined tolerances or the end products will not perform as expected.
“As multiple passes are not possible during spiral rolling, customers require a combination of power and precision in the equipment they use. Therefore, the machine must be powerful to achieve the desired capacity and accurate to achieve the required tolerances in one pass,” said Federico Bonfogo, senior technical sales manager, Faccin Group, owner of the ROUNDO brand.
ROUNDO section bending machines are designed to assist with this type of high-tolerance spiral production. Bonfogo referenced heat exchangers again to describe what the company’s technology can do in this very challenging bending application.
In heat exchangers, within the same spiral you might find tubes of different materials welded to each other. Each tube is specified for its task because each can withstand different steam pressures. Each material, however, reacts differently to stresses during bending. That means that a section bending machine used for spiral production needs to be sensitive enough to cope with each material’s springback characteristics.
In this case, Bonfogo said sophisticated hydraulics help the operator in this battle against the metal’s natural characteristics. The operator of the section bending machine can fine-tune the bend while processing the spiral to obtain a homogeneous shape.
The standard features of the ROUNDO section bending machine’s hydraulic system help to deliver this production accuracy. Operators can manipulate joysticks to control proportional movements for roll rotation and adjustment. They also can adjust variable translation speed of the calibrating unit to further fine-tune the spiral diameter after the profile has passed through the bending rolls.
For customers who demand even further precision, Bonfogo said it is possible to equip machines with a microhydraulic adjustment of the lower rolls. This allows for additional fine-tuning achieved through separated commands on the control panel and which are connected in parallel to the main roll’s adjustment.
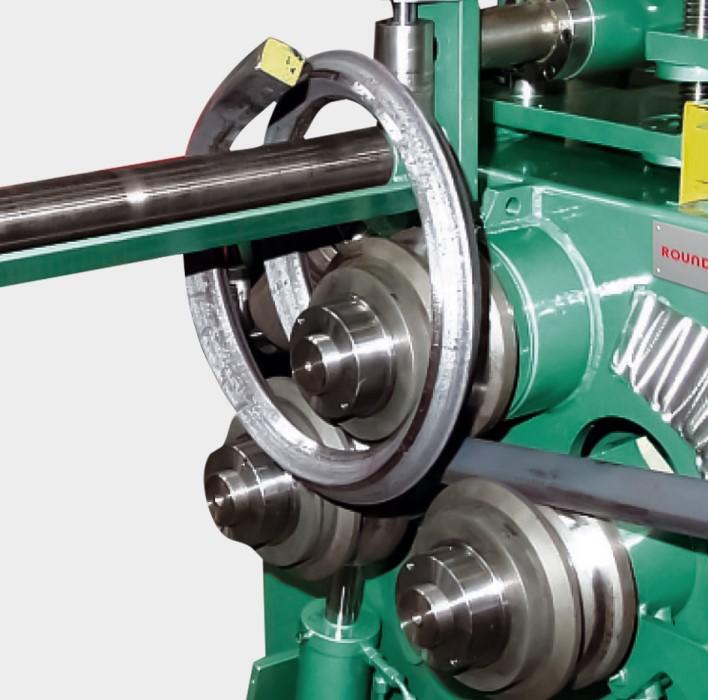
The section bending machines can be equipped with microhydraulic adjustment of the lower rolls to allow for fine-tuning of the spiral as the forming process takes place.
Spiral rolling is complicated by the fact that customers are going to ask for many different types of profiles, each with its own mechanical properties and features. Even the same type of profile may have a large variety of dimensions, which affects the rolling diameter and the pitch of the spiral as it is being fabricated.
Bonfogo said the large guide rolls on ROUNDO section bending machines act like calibrating units to ensure the desired dimensions are delivered. Moreover, each unit includes different small rolls for the calibration of different types of sections. These calibrating rolls can be placed in several positions on the frame of the calibrating units, making possible a range of bending diameters that can be calibrated.
Bonfogo said the section bending machine in its standard configuration can roll both left and right spirals without having to disassemble and reassemble the calibration unit according to the infeed side of the profile. This helps the operator to be more productive, fabricating spirals instead of spending time preparing for a different setup.
A section roll bender that not only handles standard jobs, but also can adapt easily to spiral rolling, meets the needs of those companies that run a variety of internal fabrication jobs, according to Bonfogo. The ability to move from one type of spiral fabrication to another with no additional time required for changes to the section bending machine configuration is a winning proposition for any fab shop, even those that may not have an in-house spiral form fabricating expert.
About the Author
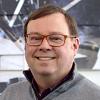
Dan Davis
2135 Point Blvd.
Elgin, IL 60123
815-227-8281
Dan Davis is editor-in-chief of The Fabricator, the industry's most widely circulated metal fabricating magazine, and its sister publications, The Tube & Pipe Journal and The Welder. He has been with the publications since April 2002.
Related Companies
subscribe now
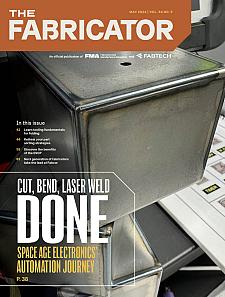
The Fabricator is North America's leading magazine for the metal forming and fabricating industry. The magazine delivers the news, technical articles, and case histories that enable fabricators to do their jobs more efficiently. The Fabricator has served the industry since 1970.
start your free subscription- Stay connected from anywhere
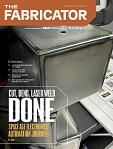
Easily access valuable industry resources now with full access to the digital edition of The Fabricator.
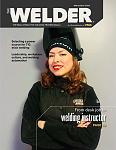
Easily access valuable industry resources now with full access to the digital edition of The Welder.
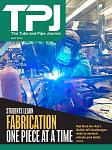
Easily access valuable industry resources now with full access to the digital edition of The Tube and Pipe Journal.
- Podcasting
- Podcast:
- The Fabricator Podcast
- Published:
- 04/16/2024
- Running Time:
- 63:29
In this episode of The Fabricator Podcast, Caleb Chamberlain, co-founder and CEO of OSH Cut, discusses his company’s...
- Trending Articles
Tips for creating sheet metal tubes with perforations
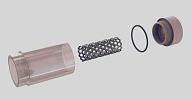
Are two heads better than one in fiber laser cutting?
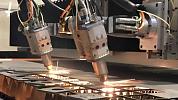
Supporting the metal fabricating industry through FMA
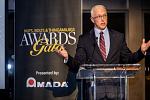
JM Steel triples capacity for solar energy projects at Pennsylvania facility
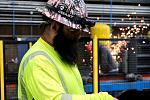
Omco Solar opens second Alabama manufacturing facility
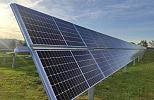
- Industry Events
16th Annual Safety Conference
- April 30 - May 1, 2024
- Elgin,
Pipe and Tube Conference
- May 21 - 22, 2024
- Omaha, NE
World-Class Roll Forming Workshop
- June 5 - 6, 2024
- Louisville, KY
Advanced Laser Application Workshop
- June 25 - 27, 2024
- Novi, MI