Product Manager
- FMA
- The Fabricator
- FABTECH
- Canadian Metalworking
Categories
- Additive Manufacturing
- Aluminum Welding
- Arc Welding
- Assembly and Joining
- Automation and Robotics
- Bending and Forming
- Consumables
- Cutting and Weld Prep
- Electric Vehicles
- En Español
- Finishing
- Hydroforming
- Laser Cutting
- Laser Welding
- Machining
- Manufacturing Software
- Materials Handling
- Metals/Materials
- Oxyfuel Cutting
- Plasma Cutting
- Power Tools
- Punching and Other Holemaking
- Roll Forming
- Safety
- Sawing
- Shearing
- Shop Management
- Testing and Measuring
- Tube and Pipe Fabrication
- Tube and Pipe Production
- Waterjet Cutting
Industry Directory
Webcasts
Podcasts
FAB 40
Advertise
Subscribe
Account Login
Search
Q&A: How sensors and controls help stampers adapt to the new normal
Remote workforce can rely on controller’s built-ins, monitoring logic, connectivity features
- By Jim Finnerty
- November 19, 2020
- Article
- Bending and Forming
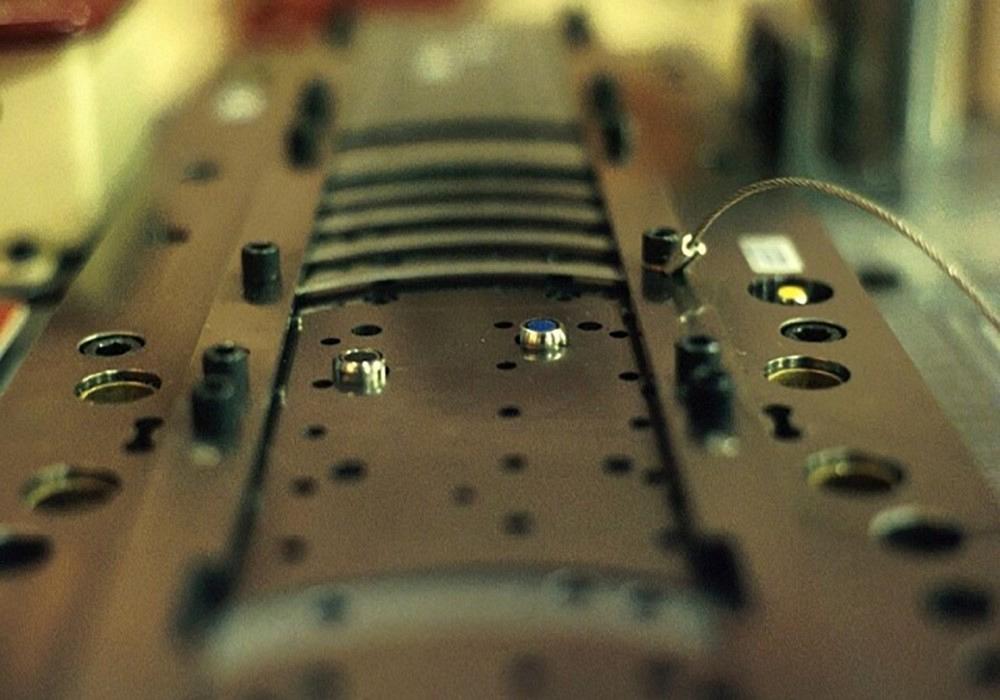
Partial feed sensing early in the cycle enables the die protection system to detect misfeeds faster.
Challenges that stampers have been facing related to the skilled worker shortage have been exacerbated by the pandemic. Stampers are trying to do more with fewer people on-site, so many of them have turned their attention to mistake-proofing and sensoring their dies and operations more.
A big problem right now seems to be training. Technical people who have never installed sensors in dies before are tasked with doing so, and they need training to be able to do it right.
There is a learning curve associated with sensoring, and bumps in the road along the way are to be expected. However, many plants are not allowing visitors, which makes training challenging. Stampers are trying to implement “new-to-them” technology sans outside help.
1. How must sensor and control systems technologies evolve to help meet these challenges?
Controls must be easier to use. Common sensor monitoring logic must be built into the controls. Sensor monitoring has to be more forgiving while still protecting the dies. Everything should be well-documented, with the documentation readily accessible for the people who need it.
2. How are sensor and control technologies addressing these challenges?
Resolving these challenges can be handled in a number of different ways:
- First, die protection courses can be an invaluable industry resource for getting stampers started with in-die sensoring. They should entail proper installation techniques, programming tips, and wiring instructions. The classes should be structured so that they can be held on-site or delivered online in shorter sessions when they cannot be held on-site.
- New die protection features that can either make the product easier to use or provide additional capability have been introduced to the market. For example, part-in-place sensors can now auto-reset when they are used for hand-fed applications. This speeds up the process because the operator doesn’t have to reset an error every time a workpiece is removed and replaced.
- Timers can be added to the sensor inputs that enable the controller to ignore short false sensor actuations while detecting the real malfunctions. When enabled, the sensor inputs are more forgiving, which helps cover up rookie implementation mistakes while still protecting the dies.
- A new type of monitoring logic allows users to monitor complex events with a single sensor input. These are events that previously required multiple sensor inputs and external timing signals. They include sensors that require multiple actuations during a single cycle; sensors that must be on at a certain angle and off at others; and sensors for gagging operations that are required to actuate on some press cycles but not others.
- Context-sensitive help screens can be present for every function in the controller. When a new operator has a programming question, they can touch a single button and get help for whatever function is on the screen at that time.
- Product manuals are a dependable resource, as long as they are updated. They should include application examples, photos and diagrams, and thorough explanations for every feature and function in the controller. The manual should be accessible at the machine, and optimally as a PDF directly in the controller that can be viewed on-screen with the touch of a button
- With so many people working remotely, it’s become necessary to provide new tools for users’ access to the controllers. To this end, full-functionality remote access features allow a company’s subject matter experts to not only view the status of the controllers, but actually program them from a desktop computer or mobile device. That way, when an operator has a programming question or application problem, the person with the answer can fix it from wherever they are, instead of having to go to the machine or try to explain it over the phone.
3. What is the future of sensoring?
The remote workforce is here to stay. Stamping manufacturers are finding that workers can be productive—sometimes even more productive—working remotely. This increases the importance of connectivity features in a controller. Remote subject matter experts with full remote access to a machine’s controls can quickly correct issues from anywhere.
Jim Finnerty is product manager for Wintriss Controls Group.
About the Author
Jim Finnerty
100 Discovery Way, Unit 110
Acton, MA 01720
978-268-2721
Related Companies
subscribe now
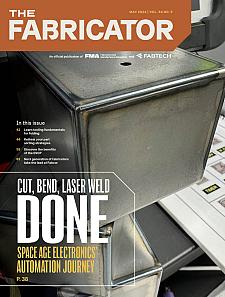
The Fabricator is North America's leading magazine for the metal forming and fabricating industry. The magazine delivers the news, technical articles, and case histories that enable fabricators to do their jobs more efficiently. The Fabricator has served the industry since 1970.
start your free subscription- Stay connected from anywhere
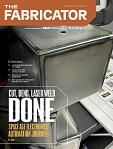
Easily access valuable industry resources now with full access to the digital edition of The Fabricator.
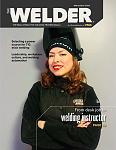
Easily access valuable industry resources now with full access to the digital edition of The Welder.
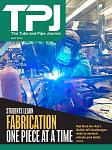
Easily access valuable industry resources now with full access to the digital edition of The Tube and Pipe Journal.
- Podcasting
- Podcast:
- The Fabricator Podcast
- Published:
- 05/07/2024
- Running Time:
- 67:38
Patrick Brunken, VP of Addison Machine Engineering, joins The Fabricator Podcast to talk about the tube and pipe...
- Trending Articles
How laser and TIG welding coexist in the modern job shop
Young fabricators ready to step forward at family shop
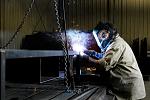
Material handling automation moves forward at MODEX
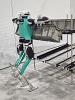
A deep dive into a bleeding-edge automation strategy in metal fabrication
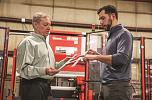
BZI opens Iron Depot store in Utah
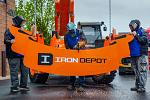
- Industry Events
Laser Welding Certificate Course
- May 7 - August 6, 2024
- Farmington Hills, IL
World-Class Roll Forming Workshop
- June 5 - 6, 2024
- Louisville, KY
Advanced Laser Application Workshop
- June 25 - 27, 2024
- Novi, MI
Precision Press Brake Certificate Course
- July 31 - August 1, 2024
- Elgin,