Editor-in-Chief
- FMA
- The Fabricator
- FABTECH
- Canadian Metalworking
Categories
- Additive Manufacturing
- Aluminum Welding
- Arc Welding
- Assembly and Joining
- Automation and Robotics
- Bending and Forming
- Consumables
- Cutting and Weld Prep
- Electric Vehicles
- En Español
- Finishing
- Hydroforming
- Laser Cutting
- Laser Welding
- Machining
- Manufacturing Software
- Materials Handling
- Metals/Materials
- Oxyfuel Cutting
- Plasma Cutting
- Power Tools
- Punching and Other Holemaking
- Roll Forming
- Safety
- Sawing
- Shearing
- Shop Management
- Testing and Measuring
- Tube and Pipe Fabrication
- Tube and Pipe Production
- Waterjet Cutting
Industry Directory
Webcasts
Podcasts
FAB 40
Advertise
Subscribe
Account Login
Search
Norton RazorStar abrasive discs designed to improve grinding performance
New grain structure aims to boost productivity and quality for metal fabricators
The Norton RazorStar discs from Norton ׀ Saint-Gobain Abrasives have engineered, shaped ceramic grain that maintains a sharp edge with each fracture of the abrasive. Because the abrasive remains sharp, a grinder operator doesn’t have to apply as much pressure as might be required with conventional abrasive discs, according to the company. Images: Norton ׀ Saint-Gobain Abrasives
Like anything being sold commercially, upgrades are necessary to keep the customer engaged. That holds true in the metal fabricating space as well, especially if you are talking about a consumable like coated abrasives.
Anyone who has been involved in removing excess weld material for the last 25 years, for example, can walk you through the changes. A bulky right-angle grinder using a small grinding wheel with fused aluminum oxide grain likely was the first tool. Then came zirconia-alumina abrasive grain that helped to reduce grinding time and extend the life of the abrasive. When the zirconia-alumina abrasive was applied to fiber discs, the market shifted toward the discs and away from the conventional grinding wheels. Next came ceramic grains on the abrasive that further reduced grinding times and offered increased abrasive life, all while requiring less force to deliver the necessary material removal rates than the previous generation of abrasive. From there, new ceramic abrasives were engineered and new topcoats, which aid in grinding performance, were developed. Today, someone in charge of cleaning up a weld likely uses a 5-lb. grinder with a ceramic abrasive fiber disc to do the job rather than the 9-lb. grinder with traditional grinding wheel of the 1990s.
The latest development in the abrasives space comes from Norton ׀ Saint-Gobain Abrasives. Its new Norton RazorStar abrasive disc comprises engineered, shaped ceramic grain with consistently sharp cutting points, even as the abrasive fractures during normal grinding use, according to Product Manager Jeremy Spencer. Aiding this ability to maintain razor-like edges is the mostly upright orientation of the grains, which keeps the sharpest points ready to dig into the material.
Even with the aggressive grain structure, the abrasive is accompanied by what the company calls a “supersized” grinding aid. This allows the abrasive to remove metal effectively while keeping the cutting action cool. This advancement also makes the abrasive suitable for use not just on carbon steel, but also aluminum, stainless steel, and nickel alloys.
Developing the New Abrasive
The RazorStar abrasive disc is the result of years of development and field testing. A Norton ׀ Saint-Gobain Abrasives team of application experts, research and development engineers, sales representatives, and suppliers helped to determine the key performance indicators that would guide the development of the abrasive. The company’s R&D team reviewed its grain production process, including an in-depth look at grain shapes that would lend themselves to being manufactured, accept a coating aid during production, and deliver the desire cutting results.
After designing, manufacturing, testing, and evaluating more than 100 prototypes and verifying performance with several field tests, the teams came up with the razor-sharp grains found on these new fiber discs, quick-change discs, and belt products. Spencer compared the new grain shape to the precision of a cutting tool found on a lathe.
“It’s very sharp, which starts with the grain’s original shape,” Spencer said. “As it fractures, it keeps fracturing at an angle so that it keeps that point. It keeps running this way until the grain’s not long enough to do the job.”
Each grain is precisely dimensioned to a patented shape. A production process is used that results in the grains’ standing upright, fully exposing the sharp edges. A resin is then applied to affix the grains to the backing and also to improve grinding performance.
The production process is very precise, according to Spencer. For example, too little resin would cause the grain to break off the base when the abrasive contacts metal, and too much resin would leave very little grain sticking out, generating more heat than is desired for the application.
The grains also are situated to the backing in precise spatial density, which helps to control the force per individual grain, according to the company. Operators of right-angle grinders now don’t have to apply as much pressure to remove metal as they might have once done with conventional abrasives.
The engineered, shaped grains on the new Norton abrasive disc are mostly oriented in an upright position.
“If the grain doesn’t fracture properly, it just stays there, collecting metal on top of it, and eventually it starts building up heat,” Spencer said.
With “capping,” as Spencer called the buildup of the metal on the grain structure, metal rubs on metal. That generates heat, leading to poor grinding results, particularly on aluminum, stainless steels, and other nickel alloys. Together, the consistently sharp grains and the abrasive’s grinding aid, which promotes less resistance during metal removal, prevent capping, and that allows RazorStar discs to be used for both carbon steel and nonferrous materials. Spencer said this might prove attractive to shops that process various metals because those doing the grinding don’t have to chase down new discs when moving from one workpiece to another.
The Results Are In
Norton ׀ Saint-Gobain Abrasives reports that internal and field testing has shown dramatic improvements in material removal when compared to standard ceramic discs on the market. In some instances, testing revealed that the new grain structure removed nearly 100% more material than the other discs and did so with less disc wear.
“We have gotten very positive reports from our field operators,” Spencer said. “They feel that it’s not trying to grab the grinder out of your hand. It’s not skating all around because the abrasive isn’t wanting to cut or that it’s so aggressive that you lose control.”
In one test conducted on carbon steel by the company, the RazorStar fiber disc removed 2,000 more grams of material than the standard ceramic grain discs. Spencer added that this type of successful material removal could allow operators doing manual grinding to use a lighter power tool than they might otherwise use. A lighter tool translates into less stress on the operator’s body over a shift.
Spencer also noted that because the engineered, shaped grains remain sharp as the abrasive is used, the fiber discs leave an attractive scratch pattern behind. Typically, when a new conventional fiber disc is put into use, the abrasives are sharp, and the scratch pattern is tight. However, as the abrasive grains wear down, the scratch pattern widens as the power tool operator applies more pressure to generate the same type of material removal that was accomplished when the abrasive grains were new and sharp.
“We have gotten a lot of positive comments about how the RazorStar discs finish,” he said.
The new abrasive is currently available in 36+ grit. The fiber discs are available in stock sizes of 4.5 to 9 in. The cloth and fiber quick-change discs are available in 2- and 3-in. sizes. The belts are made to order and are suitable for automated, impact, and off-hand grinding applications.
About the Author
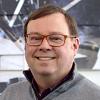
Dan Davis
2135 Point Blvd.
Elgin, IL 60123
815-227-8281
Dan Davis is editor-in-chief of The Fabricator, the industry's most widely circulated metal fabricating magazine, and its sister publications, The Tube & Pipe Journal and The Welder. He has been with the publications since April 2002.
Related Companies
subscribe now
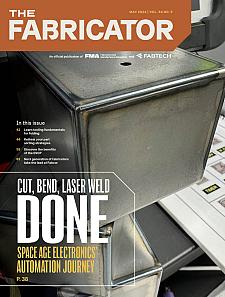
The Fabricator is North America's leading magazine for the metal forming and fabricating industry. The magazine delivers the news, technical articles, and case histories that enable fabricators to do their jobs more efficiently. The Fabricator has served the industry since 1970.
start your free subscription- Stay connected from anywhere
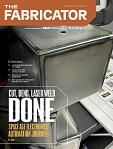
Easily access valuable industry resources now with full access to the digital edition of The Fabricator.
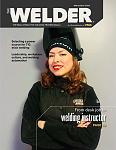
Easily access valuable industry resources now with full access to the digital edition of The Welder.
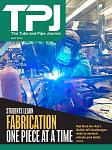
Easily access valuable industry resources now with full access to the digital edition of The Tube and Pipe Journal.
- Podcasting
- Podcast:
- The Fabricator Podcast
- Published:
- 04/16/2024
- Running Time:
- 63:29
In this episode of The Fabricator Podcast, Caleb Chamberlain, co-founder and CEO of OSH Cut, discusses his company’s...
- Trending Articles
Tips for creating sheet metal tubes with perforations
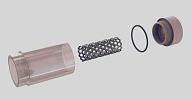
Are two heads better than one in fiber laser cutting?
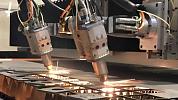
Supporting the metal fabricating industry through FMA
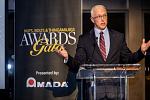
JM Steel triples capacity for solar energy projects at Pennsylvania facility
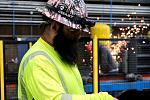
Omco Solar opens second Alabama manufacturing facility
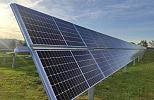
- Industry Events
16th Annual Safety Conference
- April 30 - May 1, 2024
- Elgin,
Pipe and Tube Conference
- May 21 - 22, 2024
- Omaha, NE
World-Class Roll Forming Workshop
- June 5 - 6, 2024
- Louisville, KY
Advanced Laser Application Workshop
- June 25 - 27, 2024
- Novi, MI