Contributing editor
- FMA
- The Fabricator
- FABTECH
- Canadian Metalworking
Categories
- Additive Manufacturing
- Aluminum Welding
- Arc Welding
- Assembly and Joining
- Automation and Robotics
- Bending and Forming
- Consumables
- Cutting and Weld Prep
- Electric Vehicles
- En Español
- Finishing
- Hydroforming
- Laser Cutting
- Laser Welding
- Machining
- Manufacturing Software
- Materials Handling
- Metals/Materials
- Oxyfuel Cutting
- Plasma Cutting
- Power Tools
- Punching and Other Holemaking
- Roll Forming
- Safety
- Sawing
- Shearing
- Shop Management
- Testing and Measuring
- Tube and Pipe Fabrication
- Tube and Pipe Production
- Waterjet Cutting
Industry Directory
Webcasts
Podcasts
FAB 40
Advertise
Subscribe
Account Login
Search
Beltless scrap conveying has come a long way, baby
Multiple entry points, multiple shakers, elliptical-geared, electrically operated
- By Kate Bachman
- July 9, 2015
- Article
- Materials Handling
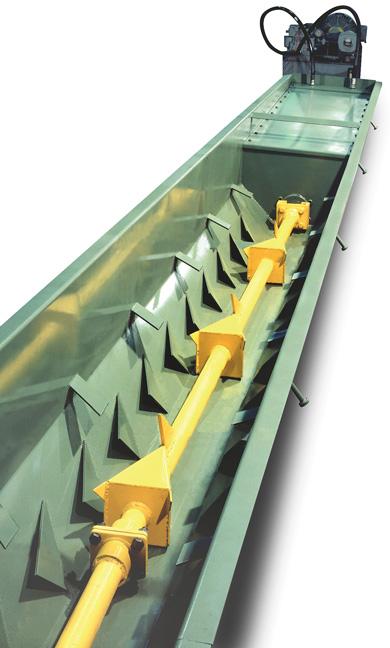
This single-drive long conveyor, which can be installed on the shop floor or, more typically, below floor grade, can handle plantwide scrap transfer with multiple inlet points. This type of conveyor system is most cost-effective if installed when a facility expands or is under new construction. Photo courtesy of PRAB, Kalamazoo, Mich.
Hemlines may rise and fall and ties may narrow and widen, but beltless conveyors are always in vogue. Magnetic slider bed, screw-type, “shaker” oscillating conveyors or vibratory conveyors have grown in popularity because of the advantages they bring and are poised to be a staple of stamping operations for years to come.
STAMPING Journal asked three leading manufacturers of beltless conveyors to explain why this type of conveyor is popular, its best applications, and what trends are showing.
1. What are the biggest advantages of “going beltless” and what are the disadvantages?
“Beltless conveyors are low-maintenance because there are fewer exposed and moving parts. The scrap material doesn’t cut the belt or get trapped under the belt surface,” said Eric Taylor, supervisor, remanufacturing services, Eriez®.
The generic term shaker conveyor tends to be used for both vibratory and oscillating conveyors, explained Pat Ontrop, sales and marketing manager for Pax Products Inc. “Vibratory conveyors use rapid back-and-forth motion to move or convey product. Typically, the material being conveyed is thrown up and forward so that it drops to the surface at a point farther down the tray.
An oscillating, or slider, conveyor cycles at a slower rate than vibratory conveyors. It advances the scrap by moving the tray forward in one direction and then sliding it back more quickly in the opposite direction underneath the part or scrap without moving the material in the opposite direction.
”Beltless conveyors provide some advantages over belted ones, depending on their type, but the reverse is true in some instances, Ontrop said (see Figure 1).
“In general, oscillating conveyors are a cost-effective solution for horizontal scrap transfer because there are up to 98 percent fewer parts in oscillating units compared to steel belt conveyors, so operating and maintenance costs are minimal,” said Prab Inc. Vice President, Sales and Marketing Mike Hill. The disadvantage of oscillating conveyors is that they cannot elevate scrap, he added.
“The mechanical vibratory conveyors are powerful vibrating machines designed for moving bulk materials over long distances efficiently,” Taylor said. The conveyors are equipped with a spring-coupled, two-mass vibrating system using a motor-driven eccentric weighted shaft to provide the exiting force to move the scrap. “A vibratory conveyor can move both magnetic and nonmagnetic materials, as long as they are on a horizontal plane,” Taylor said (see Figure 2). The option exists to use electromagnetic vibratory feeders to convey nonferrous scrap, he added.
“Magnetic slider conveyors use a continuous series of powerful ceramic magnets to pick up and glide materials along the stainless steel glider plate [see Figure 3]. Material is then discharged over the head end,” Taylor said. These conveyors can transport steel stamping scrap and stamped parts from one level to another, typically into bins or hoppers, Taylor added.
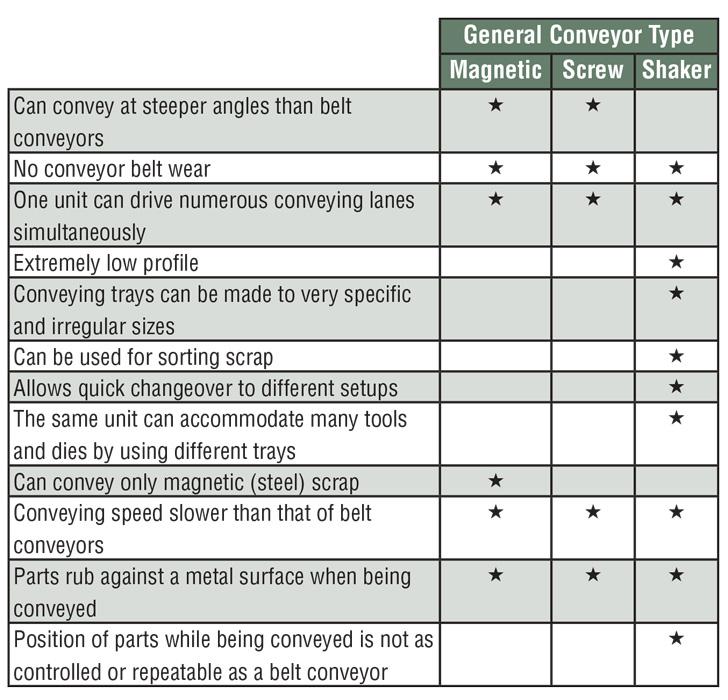
Figure 1
Beltless conveyors provide some advantages over belted ones, depending on their type, but
the reverse is true in some instances. Chart courtesy of Pax Products, Celina, Ohio.
However, because the conveyors operate on magnetic attraction of the ferrous scrap to the magnetic surface, they work in transporting only ferrous material such as mild steel, advanced high-strength steels, and ferritic stainless steel, but not austenitic stainless steel or most aluminum grades, he added.
“Incline angles can be greatly increased with magnetic conveyors over belted units [because of the magnetic pull],” Hill said.
2. What are the best applications for beltless conveyors?
“The best applications for magnetic conveyors are where a very low profile or overall conveyor height is required, a steep incline angle is necessary, or zero scrap carryover is important,” Hill said. “The best uses for oscillating conveyors involve long, horizontal scrap conveyance where zero scrap carryover is required and cost is critical.”
3. What’s new in beltless technology? Which trends are showing?
“A recent focus seems to be on long overall conveyor lengths using single drives,” Hill said (see Figure 4). In some instances, one conveyor system can handle plantwide scrap transfer with multiple inlet points, he said. “I see this trend continuing into the future.”
Taylor observed that more companies want to be sure they monetize their scrap metal whenever possible. “For this reason, Eriez’s separation technology and recycling products are designed to capture as much of the valuable scrap metal possible.”
Ontrop said he sees conveyors trending toward switching from air-driven to electric-driven shakers (see Figure 5). “Although air-operated conveyors typically have a lower purchase price and a smaller unit size, electrically operated conveyors have a lower operating cost, fewer maintenance issues, and a quieter operation than air-operated,” he said.
Ontrop also cited the following as beltless conveyor trends:
- Interconnecting the shaker to the press control
- Using shakers to remove scrap from the press and then transport it across the plant to a central or underground collection (see Figure 6)
- Using custom trays to sort scrap
- Monitoring movement of individual trays
- Using quick-connect brackets or rolling stands to facilitate quick installation and removal of unit
About the Author
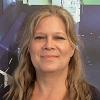
Kate Bachman
815-381-1302
Kate Bachman is a contributing editor for The FABRICATOR editor. Bachman has more than 20 years of experience as a writer and editor in the manufacturing and other industries.
Related Companies
subscribe now
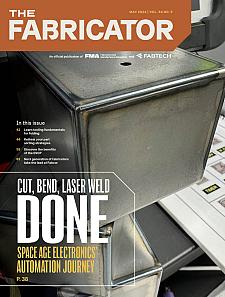
The Fabricator is North America's leading magazine for the metal forming and fabricating industry. The magazine delivers the news, technical articles, and case histories that enable fabricators to do their jobs more efficiently. The Fabricator has served the industry since 1970.
start your free subscription- Stay connected from anywhere
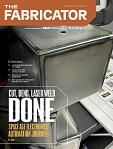
Easily access valuable industry resources now with full access to the digital edition of The Fabricator.
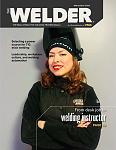
Easily access valuable industry resources now with full access to the digital edition of The Welder.
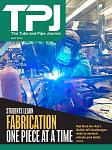
Easily access valuable industry resources now with full access to the digital edition of The Tube and Pipe Journal.
- Podcasting
- Podcast:
- The Fabricator Podcast
- Published:
- 04/16/2024
- Running Time:
- 63:29
In this episode of The Fabricator Podcast, Caleb Chamberlain, co-founder and CEO of OSH Cut, discusses his company’s...
- Trending Articles
Tips for creating sheet metal tubes with perforations
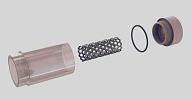
Are two heads better than one in fiber laser cutting?
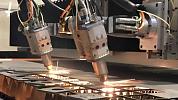
Supporting the metal fabricating industry through FMA
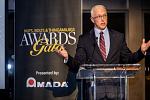
JM Steel triples capacity for solar energy projects at Pennsylvania facility
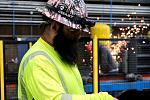
Omco Solar opens second Alabama manufacturing facility
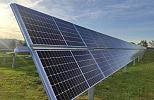
- Industry Events
16th Annual Safety Conference
- April 30 - May 1, 2024
- Elgin,
Pipe and Tube Conference
- May 21 - 22, 2024
- Omaha, NE
World-Class Roll Forming Workshop
- June 5 - 6, 2024
- Louisville, KY
Advanced Laser Application Workshop
- June 25 - 27, 2024
- Novi, MI