- FMA
- The Fabricator
- FABTECH
- Canadian Metalworking
Categories
- Additive Manufacturing
- Aluminum Welding
- Arc Welding
- Assembly and Joining
- Automation and Robotics
- Bending and Forming
- Consumables
- Cutting and Weld Prep
- Electric Vehicles
- En Español
- Finishing
- Hydroforming
- Laser Cutting
- Laser Welding
- Machining
- Manufacturing Software
- Materials Handling
- Metals/Materials
- Oxyfuel Cutting
- Plasma Cutting
- Power Tools
- Punching and Other Holemaking
- Roll Forming
- Safety
- Sawing
- Shearing
- Shop Management
- Testing and Measuring
- Tube and Pipe Fabrication
- Tube and Pipe Production
- Waterjet Cutting
Industry Directory
Webcasts
Podcasts
FAB 40
Advertise
Subscribe
Account Login
Search
Upgraded plate rolling system boosts fabricator’s output, quality
- January 16, 2024
- News Release
- Bending and Forming
Situation
Engineering and custom metal fabrication firm Membrane Process and Controls (MP&C) serves multiple sectors, including wastewater treatment and pharmaceuticals, from its Edgar, Wis., facility. Its capabilities range from the design and fabrication of stainless steel processing equipment to the installation of membrane filtration systems, CIP skids, ASME pressure vessels, atmospheric tanks, and process piping.
The fabricator recently encountered a hurdle when producing rolled tank shells. Its outdated Roundo PS-310 plate roll, which lacked CNC capabilities, no longer met the company's evolving requirements. Managing multiple operators was a challenge, and training became increasingly burdensome. The capacity of the outdated plate roller also was a limiting factor.
Always on the lookout for new technologies to enhance the effectiveness and value of its projects, MP&C knew it was time to upgrade its rolling process.
Resolution
The company reached out to Faccin Group to research new plate roller options. After careful consideration with the help of the Faccin team, MP&C decided on the Faccin 4HEL-3539 model four-roll plate roll with Siemens PGS-Ultra CNC. Top and side support completed the line for total automation.
Once that decision was made, the machine arrived within five months. “This met our timeline perfectly, as we are doubling our shop capacity, and the transition worked out well,” said Luke Stencil, maintenance supervisor at MP&C. “The day of delivery was exciting, seeing a brand new piece of equipment being placed in our facility. Our employees were eager to learn how to use the new equipment, and we knew we would put it to good use immediately.”
The machine has boosted the fabricator’s manufacturing output of tank shells and circular metal forming shapes.
“We rely on the accuracy of the machine to maintain our customers’ highest tolerances,” said Stencil. “Time and time again, it is proving itself, whether we are rolling something big or small, thick or thin.
“Right away, we are noticing an incline in quality, as this machine meets tolerances better and overall provides a better product,” he added. “The roller cuts our production time down drastically when making tank shells compared to our previous plate roll. This is incredibly helpful, as we work in a world where lead times are tight. Less time spent means less overall money spent, so the cost savings is valuable as we are able to produce more in a single day.”
Stencil also noted that the machine has been safer to work around, as most of the moving parts are contained.
Related Companies
subscribe now
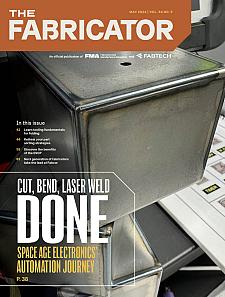
The Fabricator is North America's leading magazine for the metal forming and fabricating industry. The magazine delivers the news, technical articles, and case histories that enable fabricators to do their jobs more efficiently. The Fabricator has served the industry since 1970.
start your free subscription- Stay connected from anywhere
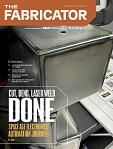
Easily access valuable industry resources now with full access to the digital edition of The Fabricator.
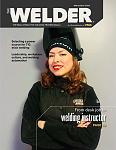
Easily access valuable industry resources now with full access to the digital edition of The Welder.
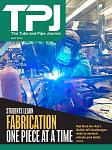
Easily access valuable industry resources now with full access to the digital edition of The Tube and Pipe Journal.
- Podcasting
- Podcast:
- The Fabricator Podcast
- Published:
- 04/16/2024
- Running Time:
- 63:29
In this episode of The Fabricator Podcast, Caleb Chamberlain, co-founder and CEO of OSH Cut, discusses his company’s...
- Trending Articles
Tips for creating sheet metal tubes with perforations
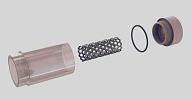
Are two heads better than one in fiber laser cutting?
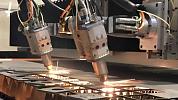
Supporting the metal fabricating industry through FMA
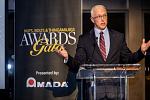
JM Steel triples capacity for solar energy projects at Pennsylvania facility
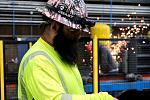
Omco Solar opens second Alabama manufacturing facility
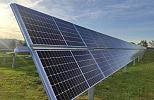
- Industry Events
16th Annual Safety Conference
- April 30 - May 1, 2024
- Elgin,
Pipe and Tube Conference
- May 21 - 22, 2024
- Omaha, NE
World-Class Roll Forming Workshop
- June 5 - 6, 2024
- Louisville, KY
Advanced Laser Application Workshop
- June 25 - 27, 2024
- Novi, MI