- FMA
- The Fabricator
- FABTECH
- Canadian Metalworking
Categories
- Additive Manufacturing
- Aluminum Welding
- Arc Welding
- Assembly and Joining
- Automation and Robotics
- Bending and Forming
- Consumables
- Cutting and Weld Prep
- Electric Vehicles
- En Español
- Finishing
- Hydroforming
- Laser Cutting
- Laser Welding
- Machining
- Manufacturing Software
- Materials Handling
- Metals/Materials
- Oxyfuel Cutting
- Plasma Cutting
- Power Tools
- Punching and Other Holemaking
- Roll Forming
- Safety
- Sawing
- Shearing
- Shop Management
- Testing and Measuring
- Tube and Pipe Fabrication
- Tube and Pipe Production
- Waterjet Cutting
Industry Directory
Webcasts
Podcasts
FAB 40
Advertise
Subscribe
Account Login
Search
Collaboration powers technology innovations for fabricating machine manufacturer
- March 27, 2023
- News Release
- Shop Management
Situation
Salvagnini designs, builds, sells, and services flexible machines and systems for processing sheet metal. Based in Sarego, Italy, the company has installed more than 7,000 systems in 75 countries for bending, punching, and laser cutting. Customized systems are delivered by 1,992 employees across five manufacturing plants, 35 service centers, and 23 operational sites to customers around the world.
“Salvagnini systems are complex,” adds Alessandro Bano, commodity manager. “They demand high quality standards and conformity with the certifications and regulations established in all of the markets we serve.”
To that end, a connected, integrated factory is a major pillar of the manufacturer’s operations. “Our aim is to create a cooperative, integrated ecosystem where machines work in synergy,” said Tommaso Bonuzzi, sales director. “This reduces the occurrence of errors while optimizing the performance of the entire production plant.”
To ensure seamless collaboration among operators, machines, and instruments, Salvagnini prioritizes the use of IIoT, cloud software, big data, and flawless interconnectivity. “We have to guarantee high connectivity standards and secure communications between on-site sheet metal machining systems and servers in the cloud,” said Bano.
High-speed connectivity not only exchanges data with factory floor systems and smart sensors, it enables a wealth of information sharing.
“Today, our machines not only communicate with the cloud to send updated production data, but they also transfer real-time information to each other and with ERP systems,” explained Bonuzzi. “The feedback from our customers on these initiatives is very positive, both in terms of greater possibilities for services and the benefits to boost the productivity of the whole process.”
For that reason, among others, Salvagnini cannot compromise on connectivity. So when the company encountered stability issues with a legacy connectivity systems provider, it reached out to Molex.
Resolution
Molex applied its knowledge of Industrial Ethernet architecture and devices to find and fix this critical problem.
Flexibility was a major consideration across the board, as the various components of Salvagnini’s systems often are adapted to different production configurations. At the same time, maintaining the typical features of standard products is prioritized to simplify sourcing and parts replacement.
“Trying to determine the root of our issue was very complicated,” Bano said. “Not only did Molex quickly analyze and solve the problem, but they offered a unique solution for Ethernet, EtherCAT, and Canbus cables, which we later adopted at all of our production sites in Italy.”
Both companies continuously work to reduce the size of connectors without compromising the reliability or quality of communications. “Another major area for us is customized solutions that require a very high mix of connecting cables with a variety of lengths and connector combinations,” noted Luciano Rosa Marin, senior business development manager at Molex.
In one case, Molex devised a plastic-injected overmold connector, which is different than conventional bayonet systems, to ensure high-speed communications stability in extremely compact environments. Another example of teamwork is a system of cameras that are installed on Salvagnini’s L3 and L5 lasers. These cameras acquire the image of a piece of sheet metal positioned on the worktable and transmit it via software as a DXF vector file to display the starting format for a new nesting.
“Of course, these cameras have to be powered continuously,” said Bano. “You also need real-time communications to send video data to the system for rapid processing.”
Molex designed a new system in which a single cable connects the RJ45 to the electrical power supply via a switch. “In addition to reducing the size and number of cables, we also improved the speed of communications performance between the camera and our system,” Bano noted.
A combined Industry 4.0 focus guides the design, development, and delivery of more compact, IP67-rated products to support increasingly smaller and more powerful machines that must perform reliably in the most rigorous environments. Opportunities to improve machine diagnostics and expedite repair times also are being explored.
“Our ultimate goal is to go beyond manufacturing and offer customized solutions to support our partners in their own evolution,” concluded Bonuzzi. “Having interconnected machines and available data to analyze and use for future choices is essential. We see huge potential for growth across the vast IIoT ecosystem, both in terms of the technical side of our systems and the business applications of our consulting services.”
Related Companies
subscribe now
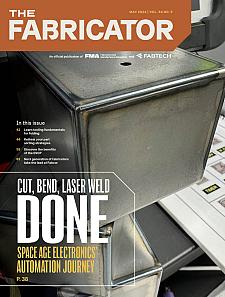
The Fabricator is North America's leading magazine for the metal forming and fabricating industry. The magazine delivers the news, technical articles, and case histories that enable fabricators to do their jobs more efficiently. The Fabricator has served the industry since 1970.
start your free subscription- Stay connected from anywhere
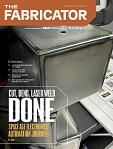
Easily access valuable industry resources now with full access to the digital edition of The Fabricator.
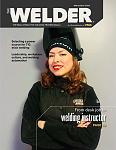
Easily access valuable industry resources now with full access to the digital edition of The Welder.
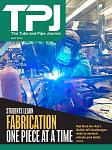
Easily access valuable industry resources now with full access to the digital edition of The Tube and Pipe Journal.
- Podcasting
- Podcast:
- The Fabricator Podcast
- Published:
- 04/30/2024
- Running Time:
- 53:00
Seth Feldman of Iowa-based Wertzbaugher Services joins The Fabricator Podcast to offer his take as a Gen Zer...
- Industry Events
Pipe and Tube Conference
- May 21 - 22, 2024
- Omaha, NE
World-Class Roll Forming Workshop
- June 5 - 6, 2024
- Louisville, KY
Advanced Laser Application Workshop
- June 25 - 27, 2024
- Novi, MI
Precision Press Brake Certificate Course
- July 31 - August 1, 2024
- Elgin,