- FMA
- The Fabricator
- FABTECH
- Canadian Metalworking
Categories
- Additive Manufacturing
- Aluminum Welding
- Arc Welding
- Assembly and Joining
- Automation and Robotics
- Bending and Forming
- Consumables
- Cutting and Weld Prep
- Electric Vehicles
- En Español
- Finishing
- Hydroforming
- Laser Cutting
- Laser Welding
- Machining
- Manufacturing Software
- Materials Handling
- Metals/Materials
- Oxyfuel Cutting
- Plasma Cutting
- Power Tools
- Punching and Other Holemaking
- Roll Forming
- Safety
- Sawing
- Shearing
- Shop Management
- Testing and Measuring
- Tube and Pipe Fabrication
- Tube and Pipe Production
- Waterjet Cutting
Industry Directory
Webcasts
Podcasts
FAB 40
Advertise
Subscribe
Account Login
Search
Risk-free tube prep for the drawing step
Automated, enclosed systems modernize chemical treatment, rinsing processes
- By Eric Lundin
- October 17, 2018
- Article
- Tube and Pipe Fabrication
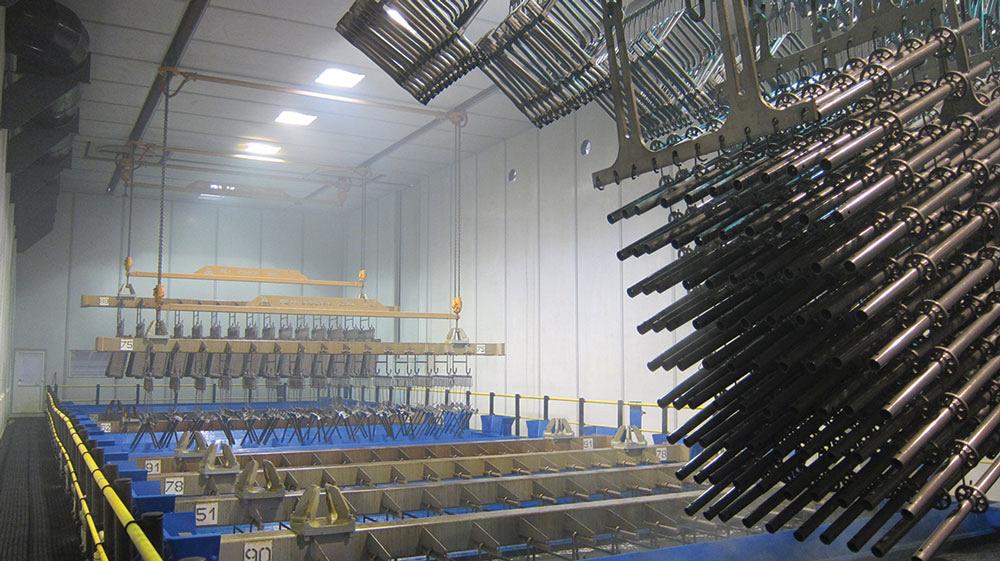
Rather than having acid tanks in the shop environment, this setup uses an enclosed area that keeps the caustic liquids and fumes separate from the rest of the shop.
Like many industrial processes, drawing a tube to change its characteristics—increasing the inside diameter, reducing the outside diameter, refining the surface, or all three—and doing it well depends on many factors. Good process control, regular die inspections and maintenance, and proper lubrication are just a few considerations.
No less important are the preparation steps. Shipments of tubing normally leave the mill bearing the remnants or residuals of mill processes, notably grease and scale. Before the tube goes to the draw benches, it needs to go through a multistage process, one comprising several chemical treatments and rinsing steps, to prepare the tube surface for the drawing process.
The chemical treatments are hazardous at best. Stored in large, uncovered tanks, the chemicals used for degreasing and scale removal are acidic, posing risks to personnel working in the immediate vicinity and to any exposed metals nearby. Health risks include exposure, inhalation, contact, and ingestion. Exposed metals are prone to corrosion from the vapors generated by the chemicals in the tanks.
“The chemical agents usually are hydrochloric acid or sulfuric acid,” said Hans Romberger, technical sales representative for Ingenia GmbH, Linz, Austria. The permissible exposure for hydrochloric acid is 5 parts per million (PPM), according to the Centers for Disease Control. For sulfuric acid, the permissible exposure is far less, just 1 PPM over an eight-hour period. Exposure to vapors or inhalation causes irritation or inflammation of the eyes, nose, and throat; difficulty breathing; and teeth erosion. Eye or skin contact with the liquid form causes mild to severe burns. Ingestion causes burns to the mouth, throat, and stomach.
Because they are intended to remove grease and mill scale from metals, these acids also are effective at cleaning any unprotected metals in the vicinity, leaving them prone to corrosion. Any metal components used in the building’s construction and in the pretreatment equipment are therefore prone to attack and corrosion. Nobody wants to see corrosion set in and begin to destroy a crane, construction beams, and other expensive items.
The exposure hazards are compounded by the number of treatment steps.
“The process usually requires three chemical stages,” Romberger said. “Each chemical stage is followed by a two-stage rinsing process.”
The first two stages involve the aforementioned acids for removing grease, scale, and rust. At this point, the metal’s surface is clean, but it’s not quite ready for a lubricant. A third chemical stage, one that imparts a phosphate coating, provides a measure of corrosion protection and prepares the surface to accept the lubricant. The phosphate coating is followed by two stages of rinsing and application of the lubricant.
“If the lubricant is a soap, the tube bundle goes from the soap-application step to a drying stage,” Romberger said. “If the lubricant is an oil, the application is followed by a draining process.”
Preprocessing Apart from Drawing
In a conventional setup, the solutions used for degreasing, descaling, and coating aren’t closed off from the shop’s environment, which is the origin of the hazard. The alternative setup uses an enclosed area to contain the reactive agents, both liquid and vapor, minimizing the risks to man and machine (see Figure 1).
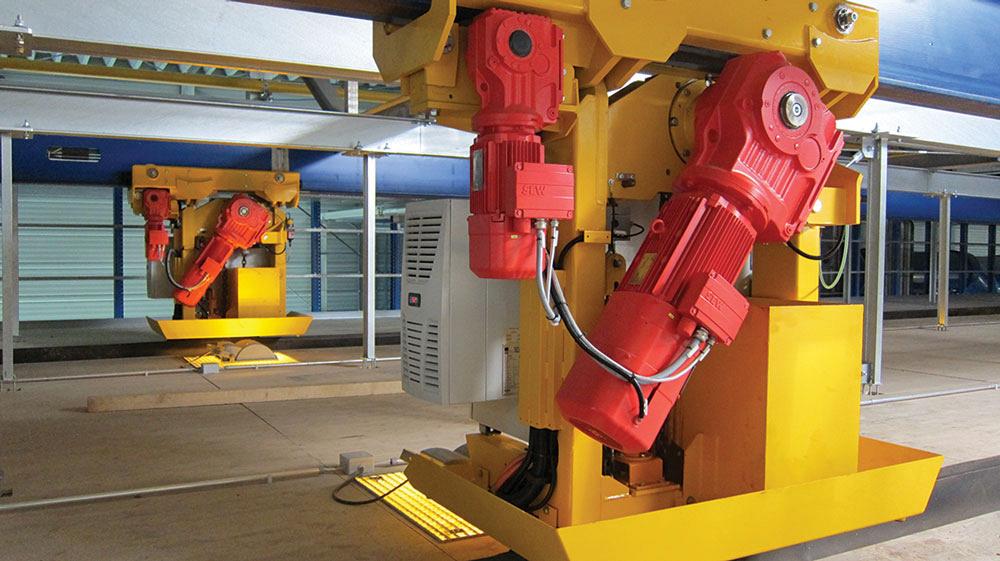
Figure 1
Containing the fumes generated by the acids used for descaling and degreasing tube is critical to prevent damage to nearby equipment. These travel units, which transfer tube bundles from tank to tank, operate at the mezzanine level and are isolated from the enclosed area below by flexible seals. Furthermore, they are protected by heavy-duty coatings and ingress-protection componentry to prevent corrosion attack.
Regarding the vapors, the systems do more than merely provide containment. The company’s pretreatment equipment includes a ventilation system that pulls a constant stream of fresh air into the processing area and sends the vapor-laden air to a scrubber unit.
“The scrubber washes out the acidic concentrates,” Rombergers said. “The clean air then is vented to the atmosphere.”
The company’s equipment likewise removes contaminants from the rinse water.
“The rinse water can be neutralized for disposal,” Romberger said. Alternatively, the company can set up a system that rejuvenates the water for reuse in the pretreatment system.
Although developing and building a new pretreatment line for new construction is usually the easiest route, the company also can replace an existing system or augment an old system to add capacity. Because the company makes nearly all of the components in-house, it has essentially unlimited latitude in designing each system individually. Tank sizes, tank locations, and the enclosed system’s layout are configured to suit the applications.
The process steps also are configurable. The operator—who isn’t an operator at all, but a programmer—determines process sequence, the pH levels for each acid stage, the immersion duration for each step of the sequence, and the drying or draining time for the last step.
Finally, because it’s an automated system, it doesn’t require direct operator involvement. No personnel are needed in the immediate vicinity of the tanks, remaining outside of the preparation area.
Ingenia GmbH, www.ingenia.at
About the Author
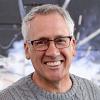
Eric Lundin
2135 Point Blvd
Elgin, IL 60123
815-227-8262
Eric Lundin worked on The Tube & Pipe Journal from 2000 to 2022.
About the Publication
Related Companies
subscribe now
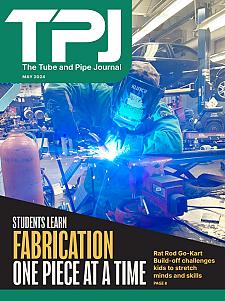
The Tube and Pipe Journal became the first magazine dedicated to serving the metal tube and pipe industry in 1990. Today, it remains the only North American publication devoted to this industry, and it has become the most trusted source of information for tube and pipe professionals.
start your free subscription- Stay connected from anywhere
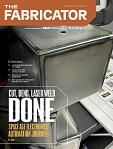
Easily access valuable industry resources now with full access to the digital edition of The Fabricator.
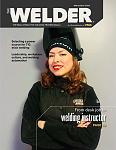
Easily access valuable industry resources now with full access to the digital edition of The Welder.
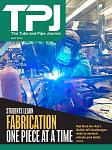
Easily access valuable industry resources now with full access to the digital edition of The Tube and Pipe Journal.
- Podcasting
- Podcast:
- The Fabricator Podcast
- Published:
- 04/16/2024
- Running Time:
- 63:29
In this episode of The Fabricator Podcast, Caleb Chamberlain, co-founder and CEO of OSH Cut, discusses his company’s...
- Trending Articles
Zekelman Industries to invest $120 million in Arkansas expansion
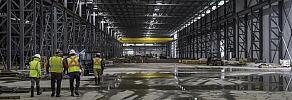
3D laser tube cutting system available in 3, 4, or 5 kW
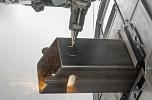
Corrosion-inhibiting coating can be peeled off after use
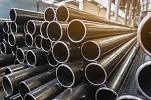
Brushless copper tubing cutter adjusts to ODs up to 2-1/8 in.
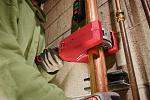
HGG Profiling Equipment names area sales manager
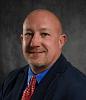
- Industry Events
16th Annual Safety Conference
- April 30 - May 1, 2024
- Elgin,
Pipe and Tube Conference
- May 21 - 22, 2024
- Omaha, NE
World-Class Roll Forming Workshop
- June 5 - 6, 2024
- Louisville, KY
Advanced Laser Application Workshop
- June 25 - 27, 2024
- Novi, MI