Director of Administration
- FMA
- The Fabricator
- FABTECH
- Canadian Metalworking
Categories
- Additive Manufacturing
- Aluminum Welding
- Arc Welding
- Assembly and Joining
- Automation and Robotics
- Bending and Forming
- Consumables
- Cutting and Weld Prep
- Electric Vehicles
- En Español
- Finishing
- Hydroforming
- Laser Cutting
- Laser Welding
- Machining
- Manufacturing Software
- Materials Handling
- Metals/Materials
- Oxyfuel Cutting
- Plasma Cutting
- Power Tools
- Punching and Other Holemaking
- Roll Forming
- Safety
- Sawing
- Shearing
- Shop Management
- Testing and Measuring
- Tube and Pipe Fabrication
- Tube and Pipe Production
- Waterjet Cutting
Industry Directory
Webcasts
Podcasts
FAB 40
Advertise
Subscribe
Account Login
Search
Tube end forms in many types and styles illustrate the process’s versatility
Forms include everything from simple reductions to leak-resistant joints
- By Pat Arens and Patrick Coenen
- April 20, 2021
- Article
- Tube and Pipe Fabrication
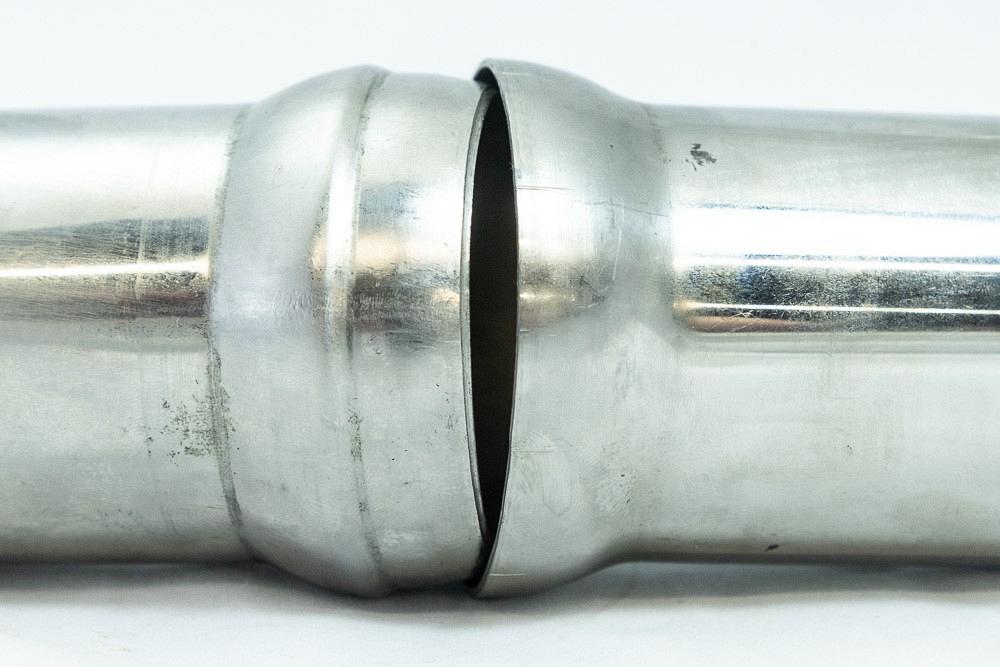
A Norma ball is similar to a Marmon joint but allows some angular displacement and is more resistant to leaking than a Marmon bead.
Nearly everyone has seen lengths of tubing with basic end forms. Some common assemblies—say, tent posts or shafts for patio umbrellas—are made from three or four lengths of tubing, each with an OD that has been reduced so it slips into the ID of the next tube. This simple example illustrates the essence of end forming: to change the tube’s geometry either at or near its end.
End forming wasn’t always a common process. Decades ago, adapters and fittings made by casting were used to join tubes for a variety of purposes. These days, rather than attach a cast fitting, it’s much more efficient to form the end of the tube to make a bead, expansion, reduction, flange, flare, groove, knurl, or a thickened wall. These operations can be done on a variety of part specifications and materials, including copper, aluminum, brass, steel, and stainless steel.
Applications and Types
Beading, the most popular type of end forming, commonly is used for automotive and heavy truck applications in which several tubes must be connected to create systems or assemblies. This assembly could be a small component such as a fuel pump or something large like an engine block. Beading isn’t a single process but several processes, and it illustrates the versatility of end forming. Unlike the simple tent pole example, formed beads can be essentially leakproof.
Beading can be done to make a Norma ball or Marmon bead. Slots are sometimes added for better joining, creating a stronger lock between the two parts.
A Norma ball, typically used to create a joint that can be adjusted before clamping,is common with 1.5- to 5-in.-OD tube. Because it’s a ball, the Norma joint allows rotation, so the user can adjust the angle of the joint based on the application and use of the tube. A Marmon bead is used for exhaust applications in the 4- to 5-in. range and uses a bead to connect to the flare, resulting in a straight coupling. Of the two, the Norma ball has the tighter tolerance and is more resistant to leaking. Flaring often is used in combination with beading. For example, a Marmon flare typically is used to mate with a Marmon bead and clamp to complete a joint between two pipes. The inside flare surface seals with the bead, working in tandem with the tensions and constraints to mate the surfaces together.
Another common flare, specifically for automotive applications, is the spherical ball flare. This is used to join with a spherical ball form and clamp, similar to the Marmon bead process. In this case, the flare and ball end-form accommodates a degree of movement to achieve the desired angle. Often used for exhaust systems in consumer vehicles, a spherical ball flare allows for minor adjustment and movement within the finished assembly.
While heavy-truck manufacturing has been a key application for end forming, other industries also rely on this family of processes. For example, residential and commercial water companies use end-formed tubing to transport fresh water and wastewater. Manufacturers in the refrigeration industry use end forms to create piping for radiators. Additionally, this process is requested by manufacturers of recreational vehicles—all-terrain vehicles, boats, motorcycles, and side-by-sides—in addition to food equipment companies, aerospace companies, and large-scale furniture makers.
Integrating End Forming with Fabrication
The end forming process often is integrated with other operations, such as bending and laser cutting, as a matter of efficiency. It reduces the material handling time, shipping time, and operational costs involved with shipping the part to an outside vendor for end forming, and it provides better quality control. By keeping all of the operations in-house and integrating end forming with other operations, better outcomes usually result.
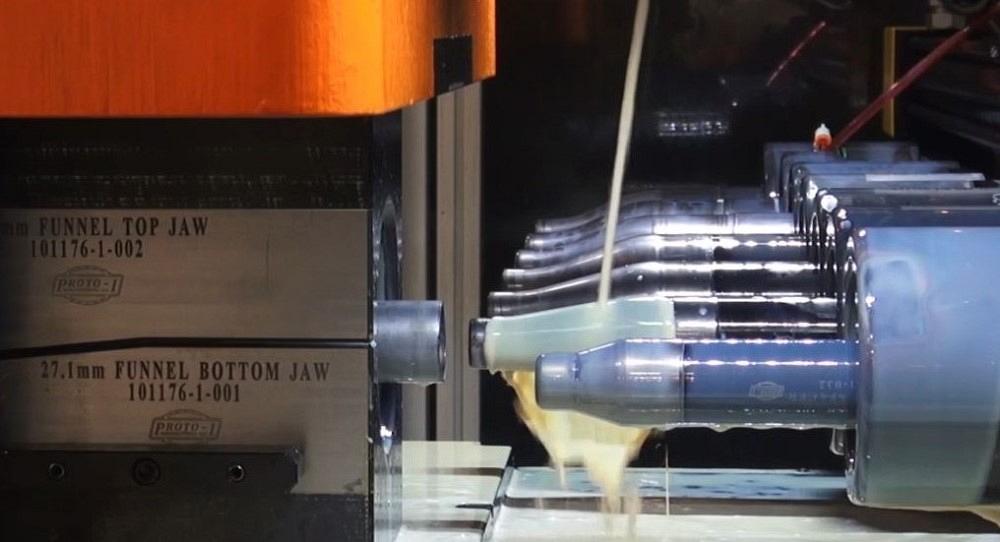
For difficult end forms, some applications call for rapid progressive forming. By making several forming steps in rapid succession on a single machine, the material does not cool between forming stages, making full use of the material’s ductility.
If bending is part of the operation, end forming can take place before or after bending, depending on the part being created and the capabilities and limitations of the other machines in the process.
If the forming work is done after bending, the tube initially is cut a little long to accommodate the processes and trimmed to the correct length when all of the processing steps are complete.
Whether done before or after bending, end forming requires a straight length for clamping to secure the workpiece. If no straight length is available after bending, a compound clamp may be necessary to get the job done. For lower-volume, one-off jobs, when cost may be an issue, an adapter can be created and welded on to help keep the part stationary.
Equipment Types
There are two primary machine types used in end forming. For lower volumes, a segmented machine, or sizer, is the most common. Its tooling has eight fingers that are powered by a mechanical drawbar, which uses pulling force on the tube or pipe to perform the expansion or reduction of the end. Segmented end forming is suitable for expansions or reductions on parts that have more generous tolerances and diameters of 1 in. and greater.
For larger volumes and tighter tolerances, spin forming machines and progressive ram forming processes are used to meet exact dimensions, concentricity, and offsets. Ram end forming is used for precise, sometimes high-pressure reducing or expanding, while progressive ram end forming uses several hits to reduce or expand the part gradually to final size without compromising the material.
Swaging, the process of reducing or tapering an object, can be done using a ram forming process to reduce a specific area or length of tube. This process also can be done using a segmented machine, changing the form of a portion of the tube; this offers increased flexibility to rotate the part during the process.
Conversely, rotary swaging typically is used for very specific projects in which the aesthetic appearance of the tube is important. It produces a highly polished form and is suitable for nondiscrete applications. The equipment used for rotary swaging is highly specialized, and the machines typically are housed in a soundproof room because they generate substantial noise while running.
About the Authors
About the Publication
Related Companies
subscribe now
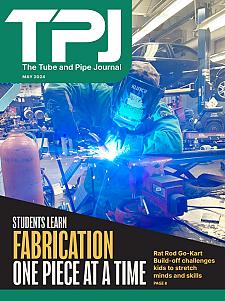
The Tube and Pipe Journal became the first magazine dedicated to serving the metal tube and pipe industry in 1990. Today, it remains the only North American publication devoted to this industry, and it has become the most trusted source of information for tube and pipe professionals.
start your free subscription- Stay connected from anywhere
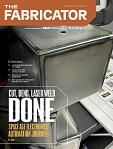
Easily access valuable industry resources now with full access to the digital edition of The Fabricator.
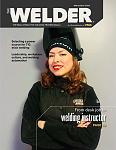
Easily access valuable industry resources now with full access to the digital edition of The Welder.
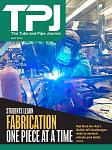
Easily access valuable industry resources now with full access to the digital edition of The Tube and Pipe Journal.
- Podcasting
- Podcast:
- The Fabricator Podcast
- Published:
- 04/30/2024
- Running Time:
- 53:00
Seth Feldman of Iowa-based Wertzbaugher Services joins The Fabricator Podcast to offer his take as a Gen Zer...
- Trending Articles
Zekelman Industries to invest $120 million in Arkansas expansion
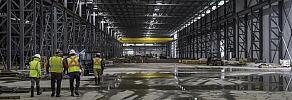
3D laser tube cutting system available in 3, 4, or 5 kW
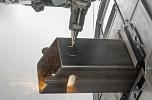
Corrosion-inhibiting coating can be peeled off after use
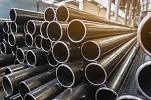
Brushless copper tubing cutter adjusts to ODs up to 2-1/8 in.
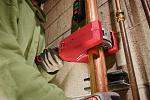
HGG Profiling Equipment names area sales manager
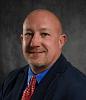
- Industry Events
Pipe and Tube Conference
- May 21 - 22, 2024
- Omaha, NE
World-Class Roll Forming Workshop
- June 5 - 6, 2024
- Louisville, KY
Advanced Laser Application Workshop
- June 25 - 27, 2024
- Novi, MI
Precision Press Brake Certificate Course
- July 31 - August 1, 2024
- Elgin,