Technical Sales & Marketing
- FMA
- The Fabricator
- FABTECH
- Canadian Metalworking
Categories
- Additive Manufacturing
- Aluminum Welding
- Arc Welding
- Assembly and Joining
- Automation and Robotics
- Bending and Forming
- Consumables
- Cutting and Weld Prep
- Electric Vehicles
- En Español
- Finishing
- Hydroforming
- Laser Cutting
- Laser Welding
- Machining
- Manufacturing Software
- Materials Handling
- Metals/Materials
- Oxyfuel Cutting
- Plasma Cutting
- Power Tools
- Punching and Other Holemaking
- Roll Forming
- Safety
- Sawing
- Shearing
- Shop Management
- Testing and Measuring
- Tube and Pipe Fabrication
- Tube and Pipe Production
- Waterjet Cutting
Industry Directory
Webcasts
Podcasts
FAB 40
Advertise
Subscribe
Account Login
Search
Automating the deburring process
Increase workplace safety, decrease operating costs
- By Mike Marshall
- January 10, 2012
- Article
- Finishing
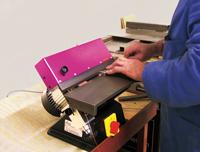
Finding a deburring machine that can fit into your fabrication scheme seamlessly can increase productivity.
Manual deburring processes have been around for years, and the people who are good at them are regarded for their expertise, manual dexterity, and skill. But it is becoming increasingly difficult to find workers who want to learn the trade or are willing to perform this less-than-glamorous job. For these reasons, many job shops are automating some of their deburring applications. The end result might also include increased efficiency, lowered operating costs, and higher profits.
Why deburr in the first place? Quite simply, we live in a time when a better fit and finish are very important. A good deburring process can provide you with both by removing sharp edges, thus producing a better finish. Too, sharp edges are a safety hazard that must be avoided at all costs. An edge that is finished properly decreases material handling costs and improves workplace safety.
Types of Burrs
A burr is an unwanted raised edge or small piece of metal that remains attached to the workpiece after a modification process. You encounter burrs anytime you use plasma, waterjet, laser, punch press, or a shear to fabricate or profile-cut sheet metal. The faster that you can finish the deburring process, the sooner you can return to fabricating.
Welding fabricators that deal with sheet metal and steel plate generally encounter two types of burrs: mechanical and thermal. Mechanical burrs are placed into three categories: Poisson burrs, rollover burrs, and breakout burrs. Rollover and breakout burrs are the most common and often are formed by shearing, punching, drilling, routing, and sawing. A tool that is sharp and set at the correct feed and speed rates can reduce the number of burrs that occur, but it won’t eliminate them altogether.
Thermal burrs, generally identified as dross or slag, occur during laser or plasma cutting. Setting the proper cutting speed and gas mixture, and using clean and well-adjusted cutting tips as well as the correct optics and gases on laser units, can greatly reduce these burrs.
Selecting a Machine to Fit Your Scheme
Before choosing a deburring method, it is important to define your desired finish requirement on the component edge. Unfortunately, no industry standard exists for a burr-free edge. Instead, the finish is determined by the specific application at hand. If you spend too much time deburring, you will drive up costs. If you spend too little time deburring, you run the risk of rework. It is very important to find the optimal balance.
Selecting the right machine isn’t merely a matter of looking at the deburring process. The machine has to fit into your overall fabrication scheme. Several tools on the market can help you to find this balance. One tool with two large-diameter, coated abrasive flap wheels turning in opposite directions performs double-sided deburring on sheet metal up to 0.2 inch thick in a single operation. It can be set up with 40-, 60-, 80-, or 120-grit flap wheels, depending on your finish requirement. For most carbon steel jobs, 40- or 60-grit flaps are sufficient, while stainless and aluminum applications require either 80- or 120-grit flap wheels.
The machine’s flap wheels can be adjusted as they wear, and one set of wheels lasts for approximately 6,500 ft. of stainless steel sheet. In addition, this type of machine can be set up in the shop either vertically or horizontally to handle the deburring operation from the top or from the side. A dust extraction port can be attached to the machine to couple with an industrial dust collection system, increasing efficiency and workplace safety.
When you need to perform deburring on thick materials, a precision beveling and faceting machine suitable for all metals can bevel parts with cross-grinding that results in zero opposite burr. This machine type can produce an infinitely adjustable beveling angle from 30 to 60 degrees and infinitely adjustable facet width from 0 to 3⁄8 in.
You might find that a beveling and deburring machine with a fixed beveling angle of 45 degrees and an infinitely adjustable beveling width from 0 to 3⁄8 in. fits your scheme. Precise adjustment of the facet width is controlled with a handwheel.
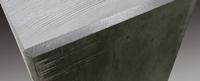
Sharp edges are a safety hazard and can result in product liability. Removing them instantly makes your work environment safer.
These machines are stationary, require little maintenance, and are operated by a single person. They run on 220- or 440-V power. If possible, try to place the deburring equipment directly into the fabrication process.
Relying on an automated deburring machine to do more of the cleanup may allow you to run your machines a little faster, increasing your output, lowering your costs, and, most importantly, improving your bottom line.
About the Author
About the Publication
Related Companies
subscribe now
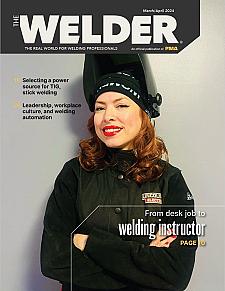
The Welder, formerly known as Practical Welding Today, is a showcase of the real people who make the products we use and work with every day. This magazine has served the welding community in North America well for more than 20 years.
start your free subscription- Stay connected from anywhere
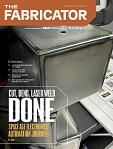
Easily access valuable industry resources now with full access to the digital edition of The Fabricator.
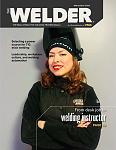
Easily access valuable industry resources now with full access to the digital edition of The Welder.
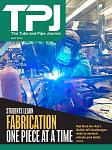
Easily access valuable industry resources now with full access to the digital edition of The Tube and Pipe Journal.
- Podcasting
- Podcast:
- The Fabricator Podcast
- Published:
- 04/16/2024
- Running Time:
- 63:29
In this episode of The Fabricator Podcast, Caleb Chamberlain, co-founder and CEO of OSH Cut, discusses his company’s...
- Trending Articles
Sheffield Forgemasters makes global leap in welding technology
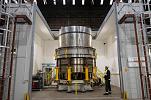
ESAB unveils Texas facility renovation
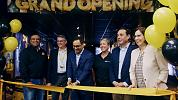
Engine-driven welding machines include integrated air compressors
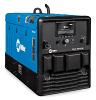
The impact of sine and square waves in aluminum AC welding, Part I
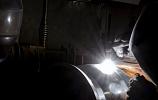
How welders can stay safe during grinding
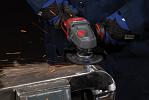
- Industry Events
16th Annual Safety Conference
- April 30 - May 1, 2024
- Elgin,
Pipe and Tube Conference
- May 21 - 22, 2024
- Omaha, NE
World-Class Roll Forming Workshop
- June 5 - 6, 2024
- Louisville, KY
Advanced Laser Application Workshop
- June 25 - 27, 2024
- Novi, MI