Editor
- FMA
- The Fabricator
- FABTECH
- Canadian Metalworking
Categories
- Additive Manufacturing
- Aluminum Welding
- Arc Welding
- Assembly and Joining
- Automation and Robotics
- Bending and Forming
- Consumables
- Cutting and Weld Prep
- Electric Vehicles
- En Español
- Finishing
- Hydroforming
- Laser Cutting
- Laser Welding
- Machining
- Manufacturing Software
- Materials Handling
- Metals/Materials
- Oxyfuel Cutting
- Plasma Cutting
- Power Tools
- Punching and Other Holemaking
- Roll Forming
- Safety
- Sawing
- Shearing
- Shop Management
- Testing and Measuring
- Tube and Pipe Fabrication
- Tube and Pipe Production
- Waterjet Cutting
Industry Directory
Webcasts
Podcasts
FAB 40
Advertise
Subscribe
Account Login
Search
User-friendly software lessens the learning curve for high-tech welding, cutting equipment
How equipment manufacturers are simplifying welding-related software for fab shops
- By Rafael Guerrero
- June 8, 2023
- Article
- Arc Welding
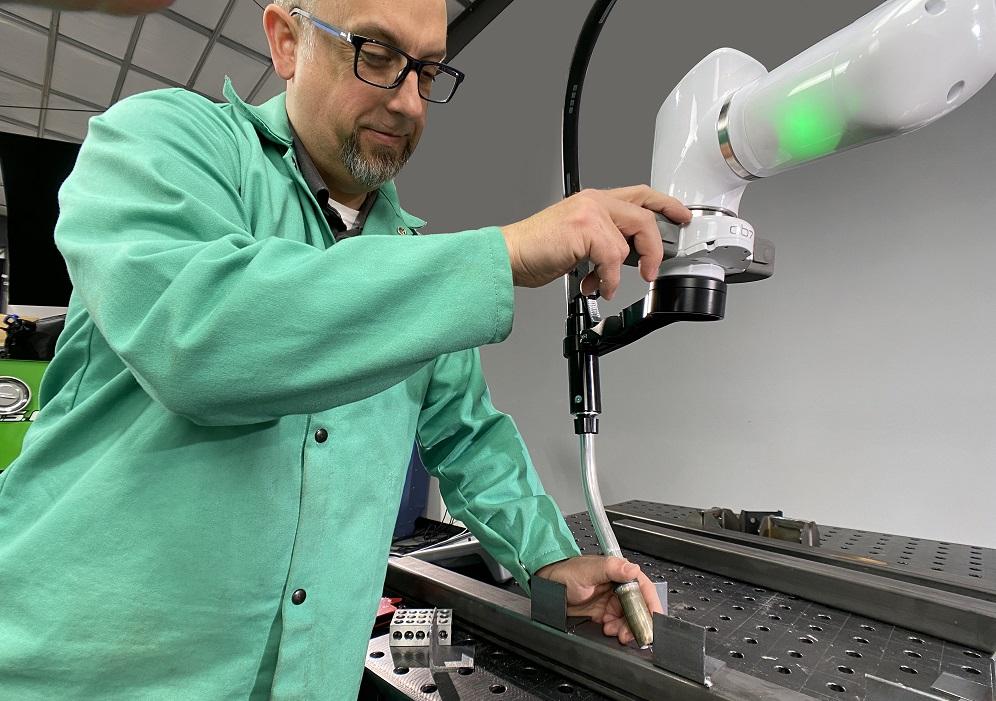
The no-programming approach Productive Robotics adopted for its welding cobot means users teach the robot how to weld certain parts rather than program the process. Productive Robotics
Shops today must maneuver a changing environment that includes an aging workforce, a shortage of skilled tradespeople (including welders), and rapid technology improvements.
Welding-related advancements add another layer to the complexities of running or working in a shop today. Those advancements have forced shops to ponder a few questions: Can I afford to bring in a cobot? Will it solve any parts production or labor issues I may have? Can my employees learn to operate a cobot quickly without it becoming a disruption?
Welding products and equipment manufacturers are asked these questions all the time. In fact, the answers help shape how these companies simplify and improve the user interface of cobots, CNC plasma cutting tables, and other tech-based welding-related tools and equipment.
Three equipment manufacturers shared how they have made some of their software and user interfaces more user friendly, less intimidating, and more efficient to help shops and fabricators maintain productivity.
“Many job shops don’t have people that have programmed robots before, they just don’t have the large pool of technical resources to pull from that, for example, automotive OEMs and suppliers have,” said Josh Williamson, global product manager, welding, ABB Robotics. “It’s very important to make robotic welding user friendly and easy.”
Start and End Points
At FABTECH 2022, ABB Robotics and Lincoln Electric unveiled their recent collaboration—a gas metal arc welding (GMAW) package featuring ABB’s GoFa CRB 15000 cobot and the Lincoln Power Wave R450 robotic power source.
“We’re targeting small to medium job shops that have relatively low-volume batches. Our goal is to make it as easy as possible to transition from part to part,” Williamson said. “If they’re welding part A and switch over to part B for a week, we want to make it easy to go back to part A. Simply put back part A and its fixturing and call it back up from the robot controller and run it again.”
ABB and Lincoln packaged the system with software they say is among the easiest to use and master in the realm of robotic welding cells. Once a user inputs information like material type, material thickness, wire diameter, and shielding gas, the interface determines the welding parameters and travel speed using a built-in welding library. The user then manually guides the cobot torch to the starting and ending weld points, with the software and package recording the movement. An intuitive software interface walks users through the entire process.
Once this process is complete, the robot is ready to work.
“You only really need to program the weld start, continue, and end points. The other points are programmed through path memorization and lead-through programming,” Williamson said.
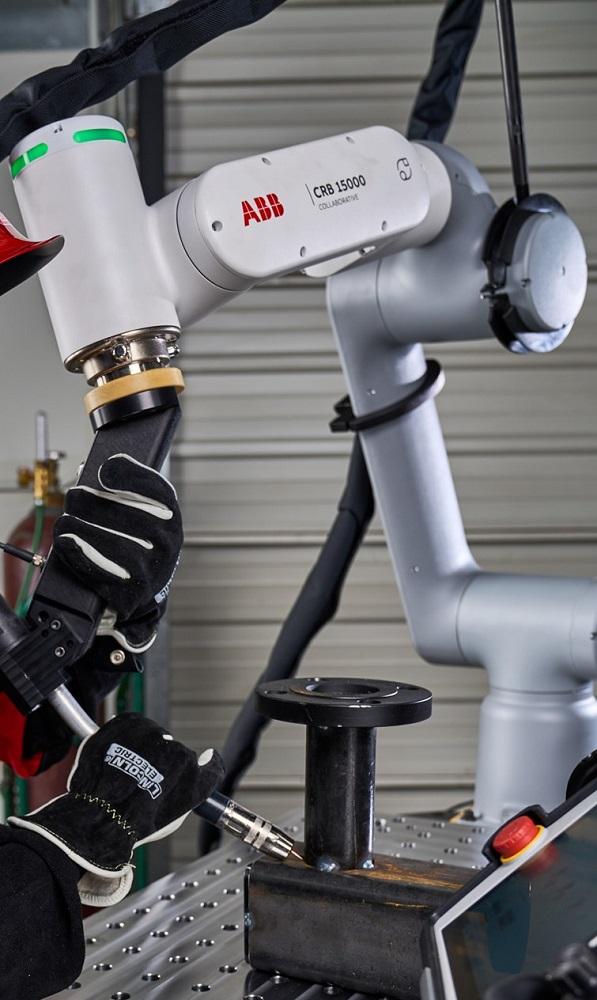
ABB Robotics and Lincoln Electric’s cobot package includes user-friendly software and an interface that walks users through the process of operating the cobot. Some users were ready to weld in less than an hour. ABB Robotics
The software interface allows users to weld with the cobot quickly—much faster than expected, he added.
“A partner of ours slotted in the better part of a day to train several potential customers, but after 30 minutes they basically had learned the programming process and were running on their own without any support. The trainers were just watching and making sure they were available to answer any questions,” Williamson said.
Because the software is easy to learn and use, job shops do not have to significantly disrupt operations for training, he said.
ABB and Lincoln sent the system out for testing, with the robotic package and software tested by both experienced tradespeople, like welders, as well as people outside of the trades. A shipping and receiving employee with no robotics experience had no problems programming the cobot, Williamson said of one test.
While this robotic package does need someone who can identify a good weld from a bad weld, this collaboration is designed for people less experienced in welding and/or programming.
No Programming Required
Productive Robotics has made a name for itself with its cobots geared toward CNC machining, medical manufacturing, food and beverage, and other industries before recently entering welding automation.
Its Blaze robotic welding systems employ a no-programming approach to cobot use. Users teach the OB7 robot how to weld certain parts, rather than program the process, Productive Robotics President Zac Bogart said.
The operator grabs the robotic arm, uses buttons on the arm to dictate how and where it should move, and selects a “recipe” the robot will follow. Bogart said a person can learn how to operate the robot in an hour or less.
“You teach the robot, you tell it what recipe to execute,” he said. “That really tells the welder everything about what it needs to know to do that kind of a weld. There are things such as the control of the gas, the voltage and current the welding is being done with, the speed that the welder is operating with, the type of electronic controls.”
He continued: “We’re able to build the welding software directly inside our main robot software ... we’re not just buying an off-the-shelf collaborative robot and putting a little bit of software on top of it. Our software is integrated all the way through.”
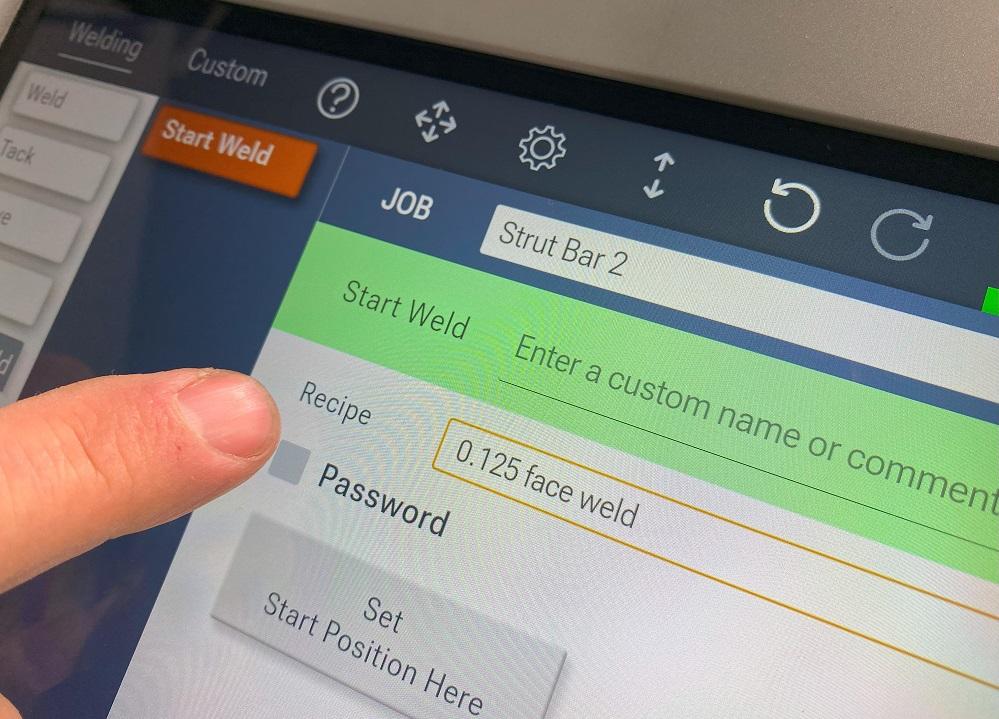
Welding software and user interfaces have become easier to learn and use—a boon for shops as they consider ways to improve productivity, adapt to new technologies, and deal with the shortage of workers. Productive Robotics
Bogart said they wanted to make sure this robotic cell performs to the level expected from shops and seasoned welders. However, the company also had ease of use in mind because a simple robotic welding user interface is important for shops.
“The industry really has two things going against it. Trying to reshore production but also, at the same time, it’s very difficult to hire people. Put on top of that trying to hire experienced welders, it gets even worse,” he said.
Easier to Cut
The 4- by 4-ft. and 4- by 8-ft. plasma cutting tables from Airgas’ RADNOR brand come equipped with FlashCut CNC’s FlashCut software, used in industrial applications as well as in metal artwork.
What was once considered software for hobbyists, smaller projects, and the arts has become so much more, said Bill Pharmer, national sales manager for advanced fabrication at Airgas. Customers appreciate the flexibility of FlashCut, its integration of other components like CAD, and its ease of use, like the “setup wizard” that comes right out of the box.
“All you have to do is plug it in and have your software loaded on your laptop and it will walk you through the setup step by step. In an hour or so, after putting all the hardware together, you’re up and running,” Pharmer said.
In a couple of hours, a user can learn FlashCut to cut simple parts; more complex projects may take a bit more time, Pharmer said. DWG and JPG files can be imported to make those projects easier.
Nonetheless, the software has the less tech savvy in mind. In one real-world example, Pharmer taught someone who knew nothing about Microsoft Windows how to use the plasma cutting software. In a matter of hours, the person was cutting parts.
Easy-to-use software helps shops work through a number of issues, like labor shortages, roles, and responsibilities.
“It speaks to this labor shortage in savings,” Pharmer said. “There’s a lot of smaller, mid-size customers that don’t have an engineering department. If they can train and get their operators up to speed with the software, they can go from design to cut right on that software without having to go through an engineering department.”
He continued: “At the end of the day, you want to be hiring people to produce parts, you don’t want to be training them to be programmers or CAD engineers. But if you can compress the time it takes to train someone new, not only does it help you with the labor shortage, but it also helps you with producing parts. A lot of the advanced features in the software speak to exactly what’s happening on the table ... just teaching the person how to run it easily increases productivity.”
About the Author
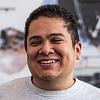
Rafael Guerrero
2135 Point Blvd.
Elgin, IL 60123
(815)-227-8242
Rafael Guerrero. was named editor of The Welder in April 2022. He spent nine years as a journalist in newspapers in the Midwest and Pacific Northwest, covering topics and communities in central Illinois, Washington, and the Chicago area.
About the Publication
Related Companies
subscribe now
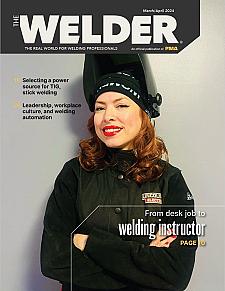
The Welder, formerly known as Practical Welding Today, is a showcase of the real people who make the products we use and work with every day. This magazine has served the welding community in North America well for more than 20 years.
start your free subscription- Stay connected from anywhere
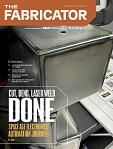
Easily access valuable industry resources now with full access to the digital edition of The Fabricator.
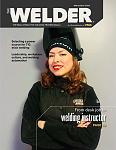
Easily access valuable industry resources now with full access to the digital edition of The Welder.
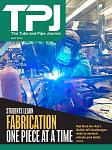
Easily access valuable industry resources now with full access to the digital edition of The Tube and Pipe Journal.
- Podcasting
- Podcast:
- The Fabricator Podcast
- Published:
- 04/16/2024
- Running Time:
- 63:29
In this episode of The Fabricator Podcast, Caleb Chamberlain, co-founder and CEO of OSH Cut, discusses his company’s...
- Trending Articles
Sheffield Forgemasters makes global leap in welding technology
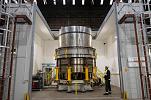
ESAB unveils Texas facility renovation
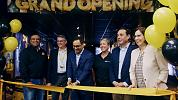
Engine-driven welding machines include integrated air compressors
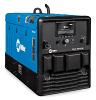
How welders can stay safe during grinding
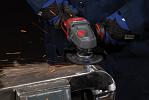
The impact of sine and square waves in aluminum AC welding, Part I
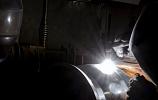
- Industry Events
16th Annual Safety Conference
- April 30 - May 1, 2024
- Elgin,
Pipe and Tube Conference
- May 21 - 22, 2024
- Omaha, NE
World-Class Roll Forming Workshop
- June 5 - 6, 2024
- Louisville, KY
Advanced Laser Application Workshop
- June 25 - 27, 2024
- Novi, MI